It’s gone! The rusted out septic tank that’s been part of our property for years is finally gone to the scrap yard!
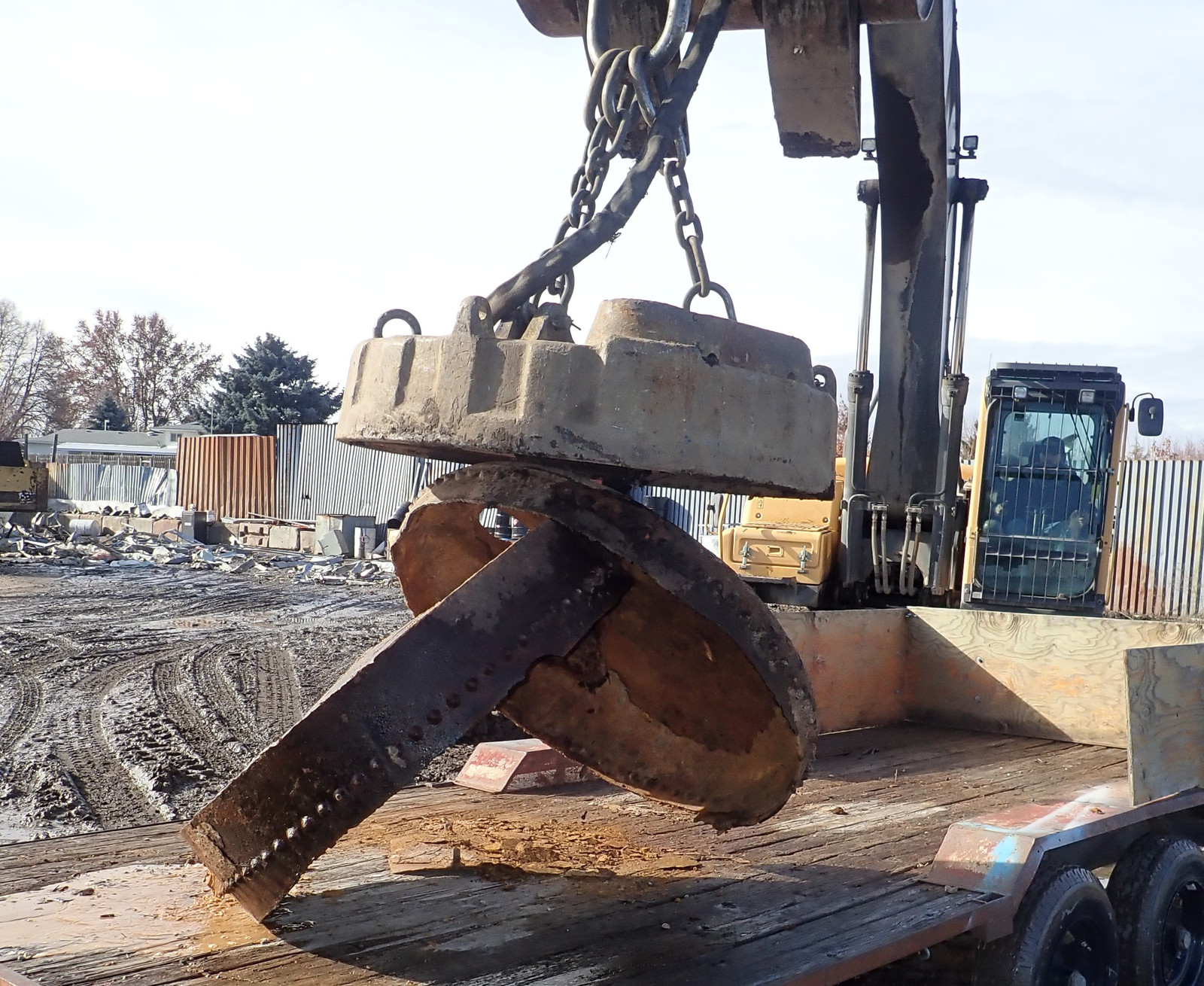
When we moved onto the hill, we knew there was an old buried septic tank underground that should probably be removed at some point. It wasn’t anything you’d recognize as a septic tank - it was more “an old underground gas tank, or something like that, used as a septic tank for some while.” Totally not to code, totally not the slightest bit acceptable as a septic tank by modern standards, but it also worked for an awful lot of decades. However, being “a void under the hill of absolutely no use to us,” I did want it gone. And about eight years later, it’s finally gone.
Knowing That Guy
Can I say I really like living in Idaho, versus the Seattle area? There’s no shortage of people in my social circles out here who can do a wide range of things, and we tend to trade skills and projects around. One of the skills I lack (almost entirely) is “high temperature metalworking” - welding, cutting, etc. It’s on my list of things I’d like to learn, but when you have a bunch of people around who can do those things, it’s slightly less important to be able to do them yourself. I’ve traded things like server builds for such work.
Here, I’m using a friend of mine (Josh) and his business, Pig Iron Rose. He’s local to the Treasure Valley in Idaho (Nampa, Boise, Meridian, Caldwell, etc), and if you have a need for lawn services or general “weird problem solved” services, look him up!
The Tank
Some years back, we had someone out doing ground work, and they were confident they could crush the tank in with their excavator. This is apparently normal enough for old tanks - just beat them into a solid mass and backfill over them.
The excavator bounced off the tank. This wasn’t going to work.
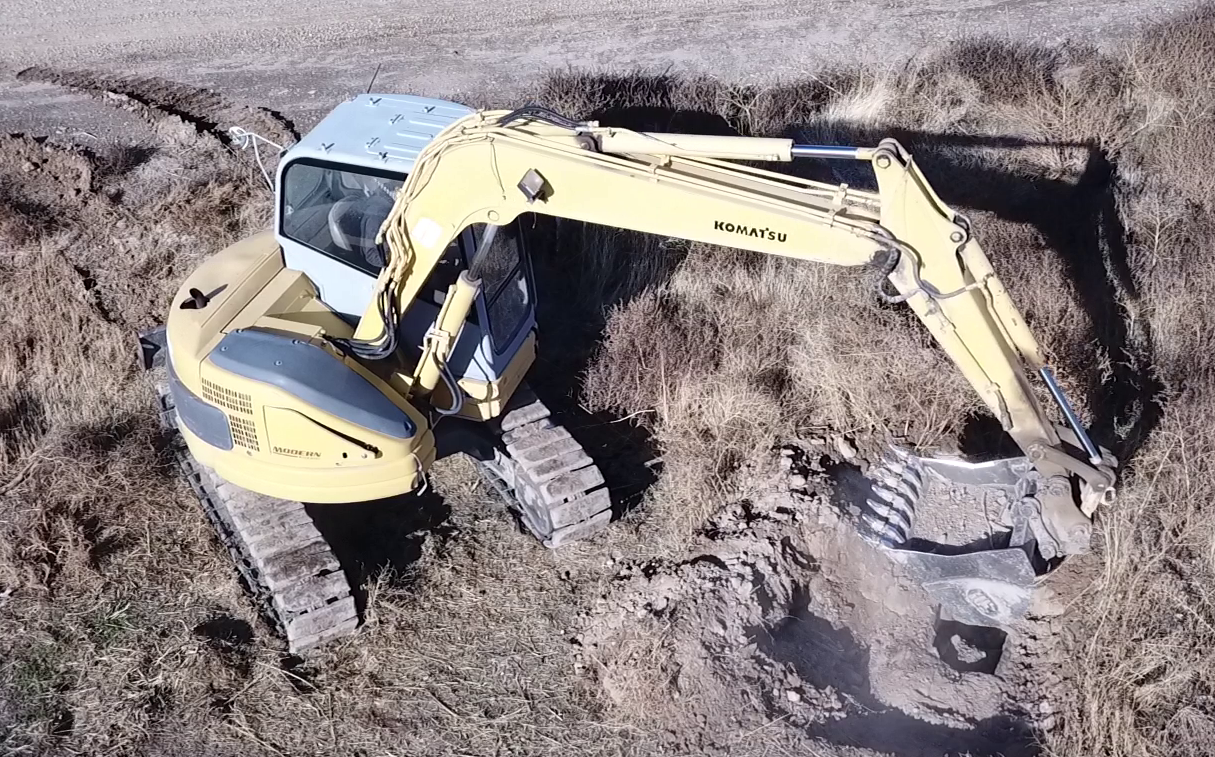
We later had someone else out with a decent sized backhoe (putting in a retaining wall), and they were able to dig the tank up and pull it out of the ground. It was half full of dirt or septic remains or something, and they couldn’t move it further, but it was at least up where it could be worked on - and there it sat for several years, because quite a few people looked at it, and commented about just how awful cutting that thing apart would be. I don’t know my way around a cutting torch, and a rusted, caked up tank of massive thickness didn’t seem a good one to learn on.
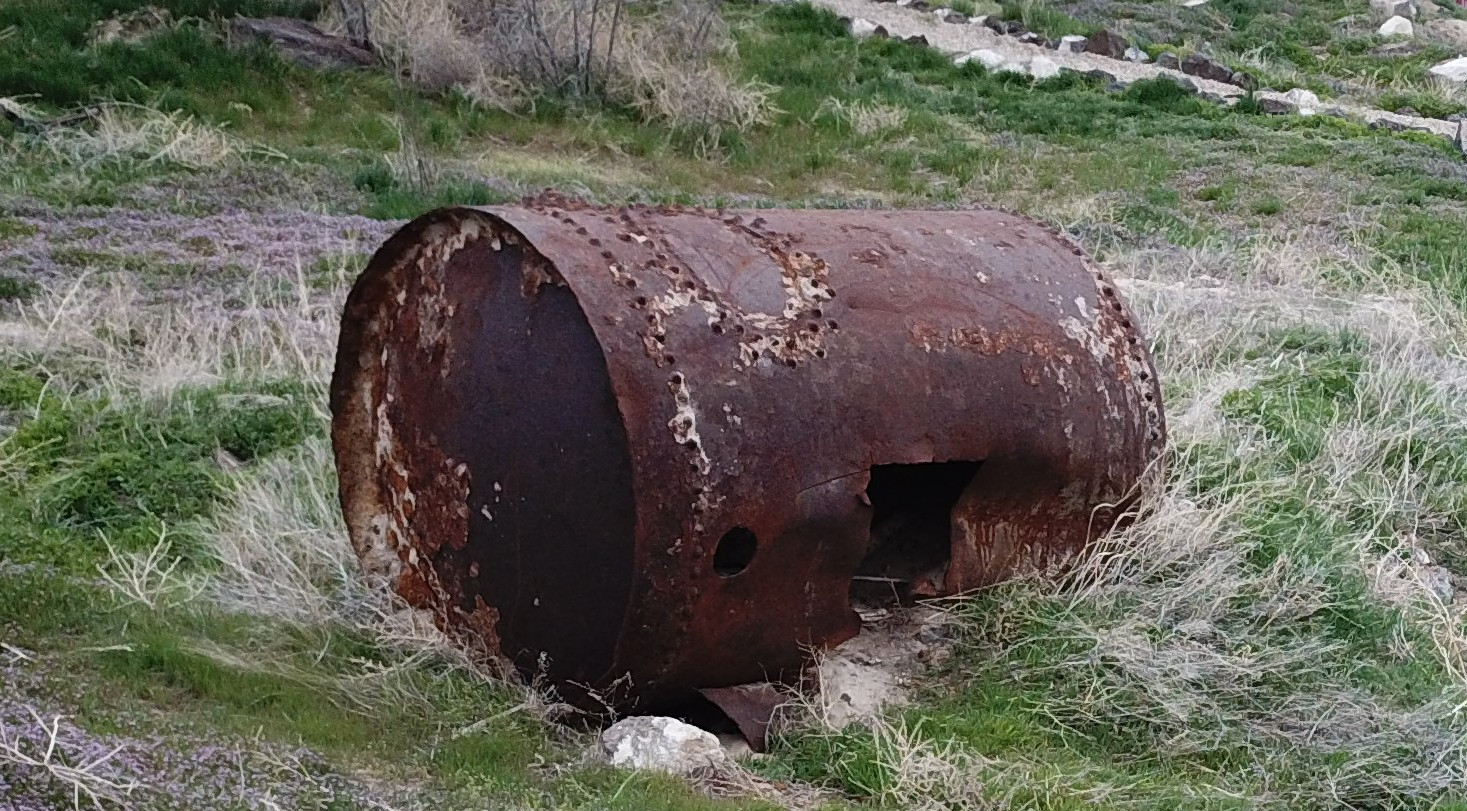
Cutting it Up
There’s also the problem of “Not lighting our hill on fire.” There have been times when people were free to help cut the tank up, but it was “windy and dry” - and while I have some good hoses, I would still like to avoid “making the list” of people who’ve lit the hill on fire. Instead, I waited until things were good and wet in the winter - though we got an awful lot more snow after this. The ground was wet, the wind was calm, and Josh was here with a set of tanks strapped into the back of his truck. Time to start carving!
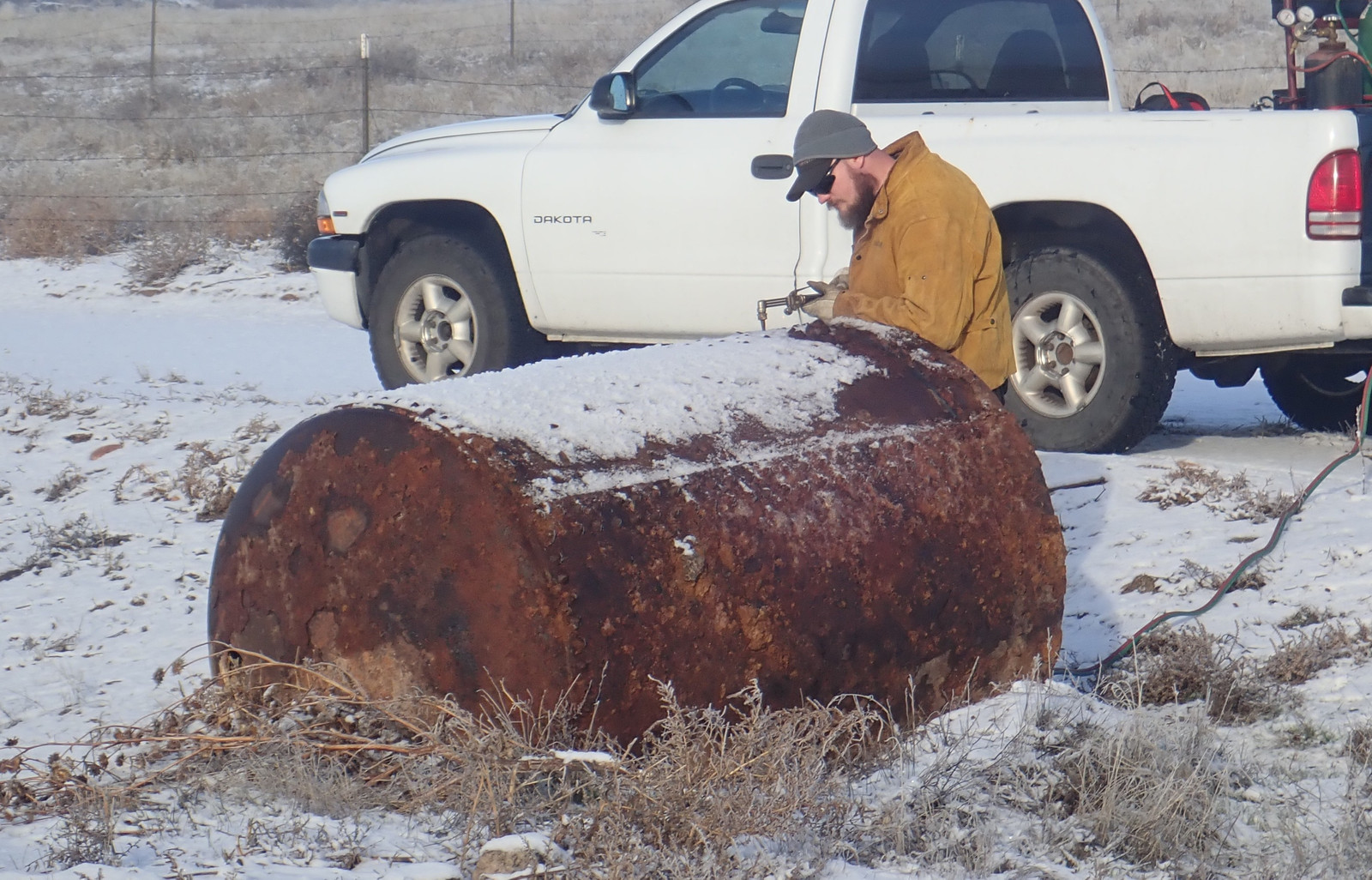
The tank is quarter inch plate steel, with a lot of overlapping riveted joints in it. Also, the inside is covered with a layer of rust, dirt, and a variety of other things that mean it’s a hard cutting pain in the rear. Torches like to be able to cut through stuff, and the backside of this is a rather torch-proof layer.
After talking through sizes, we decided to break it into large pieces that can be handled by “a few guys lifting” - no need to make it small, it’s just going to the scrap yard. But we did need to get enough of it opened up to empty out the remains. I’d tried to empty it through the access hole, and it just wasn’t working - there wasn’t enough access port size to be able to clear out much of what was in it.
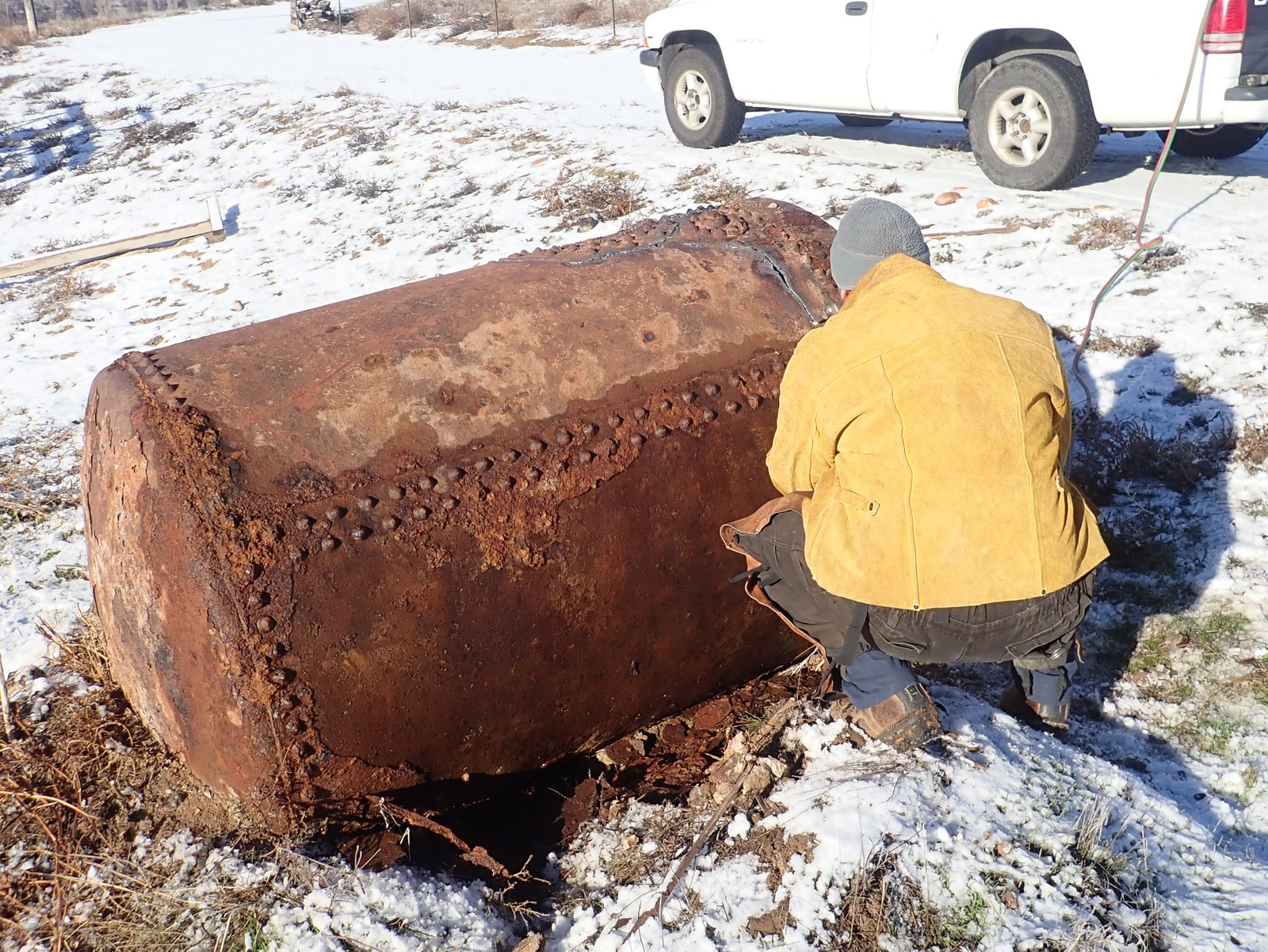
After some experimentation, we discovered that “whaling on the tank with sledgehammers” helped break up some of the crud on the inside and improved the cut, at least somewhat. However, as you can see here, that doesn’t prevent it from finding more junk and making a molten puddle of metal on the surface. I’ll show you later what it should look like when everything is working smoothly.
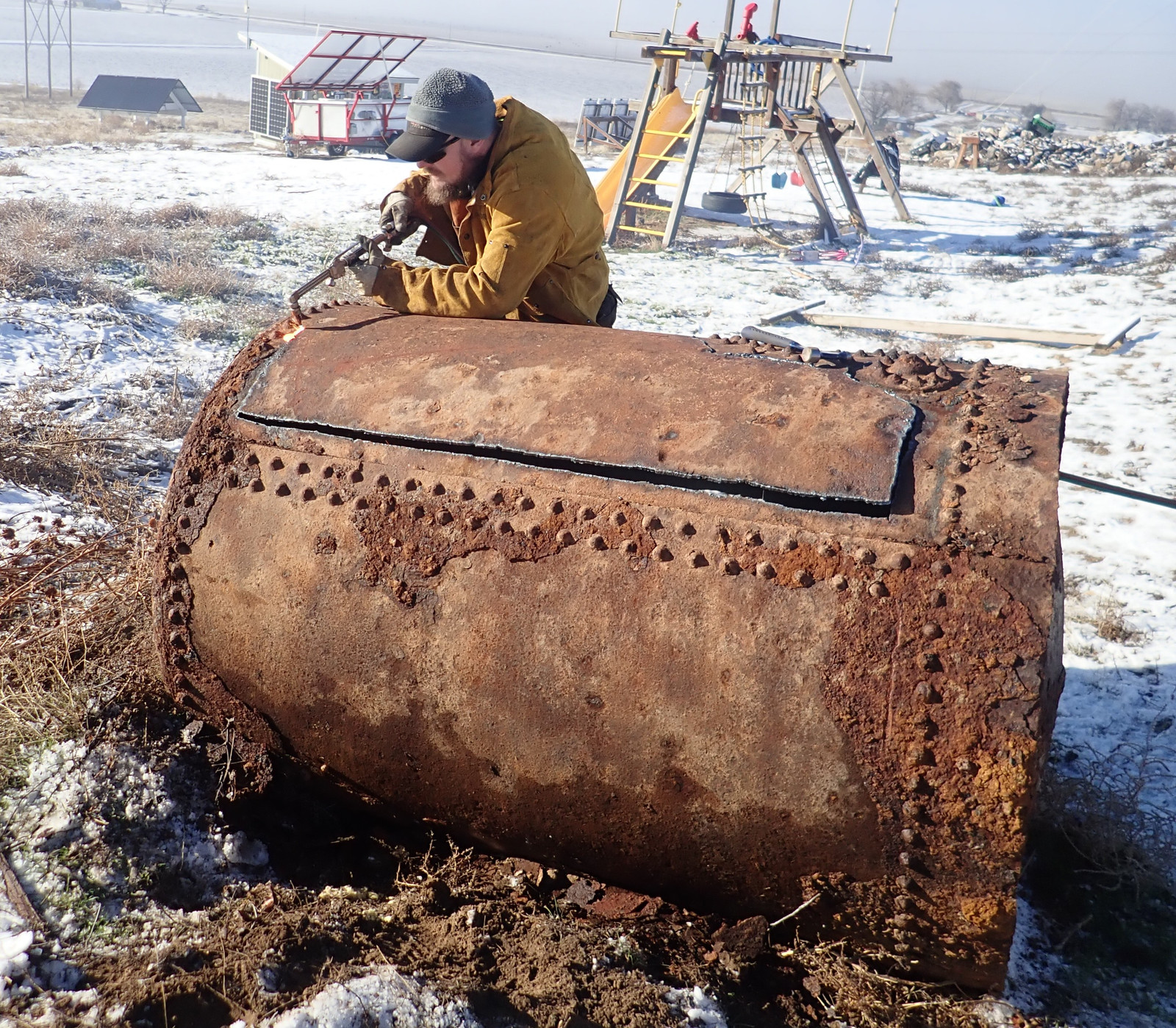
Once the cuts are almost through, you can start bending the metal away and make the final cuts easier. See all that crud on the inside of the metal? That’s what’s making the cutting hard - and this is after driving most of it off with hammers from the outside. We did a solid rendition of the Anvil Chorus while bashing away at it!
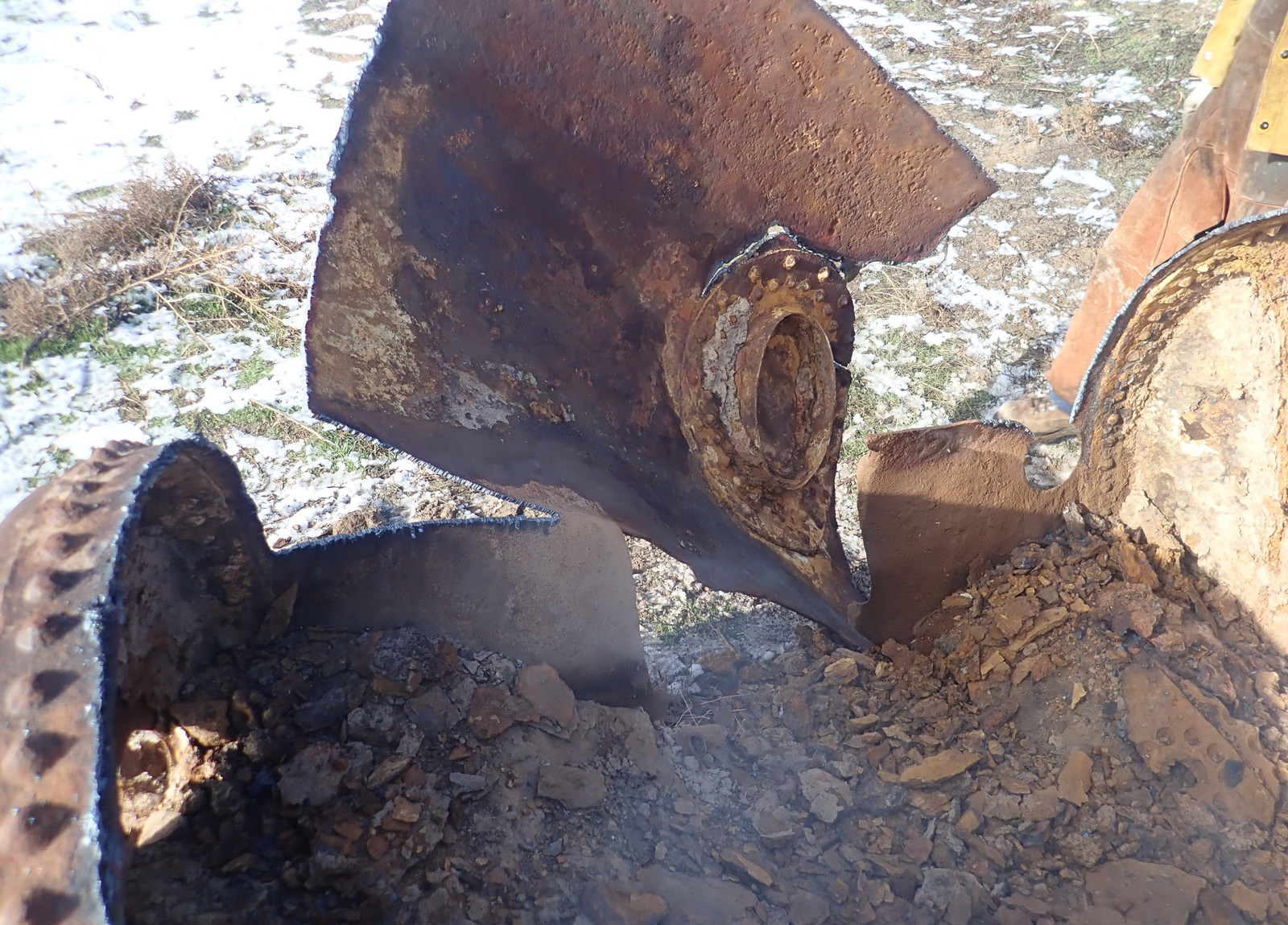
I promise you, this is just as nasty as it looks. It’s caked mud, rust, septic remains, and… I’ve no idea what else. But it does not cut. Not in the slightest.
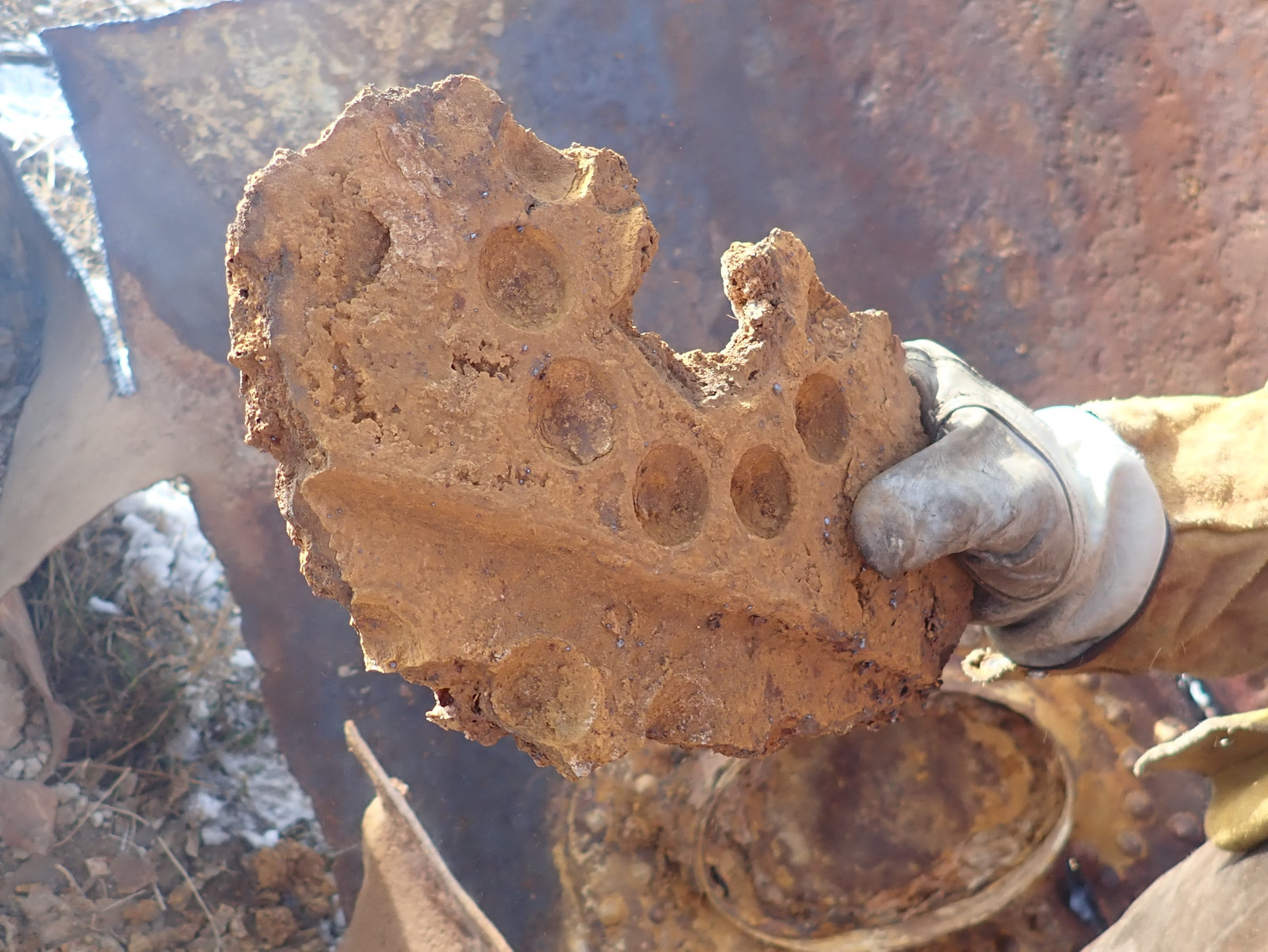
This tank is from before things were welded together - it’s proper ancient boilermaking. This access port is a large metal flange, riveted in place. I have to assume the people who were inside the tank didn’t have hearing protection when this was built, which just sounds awful. Literally!
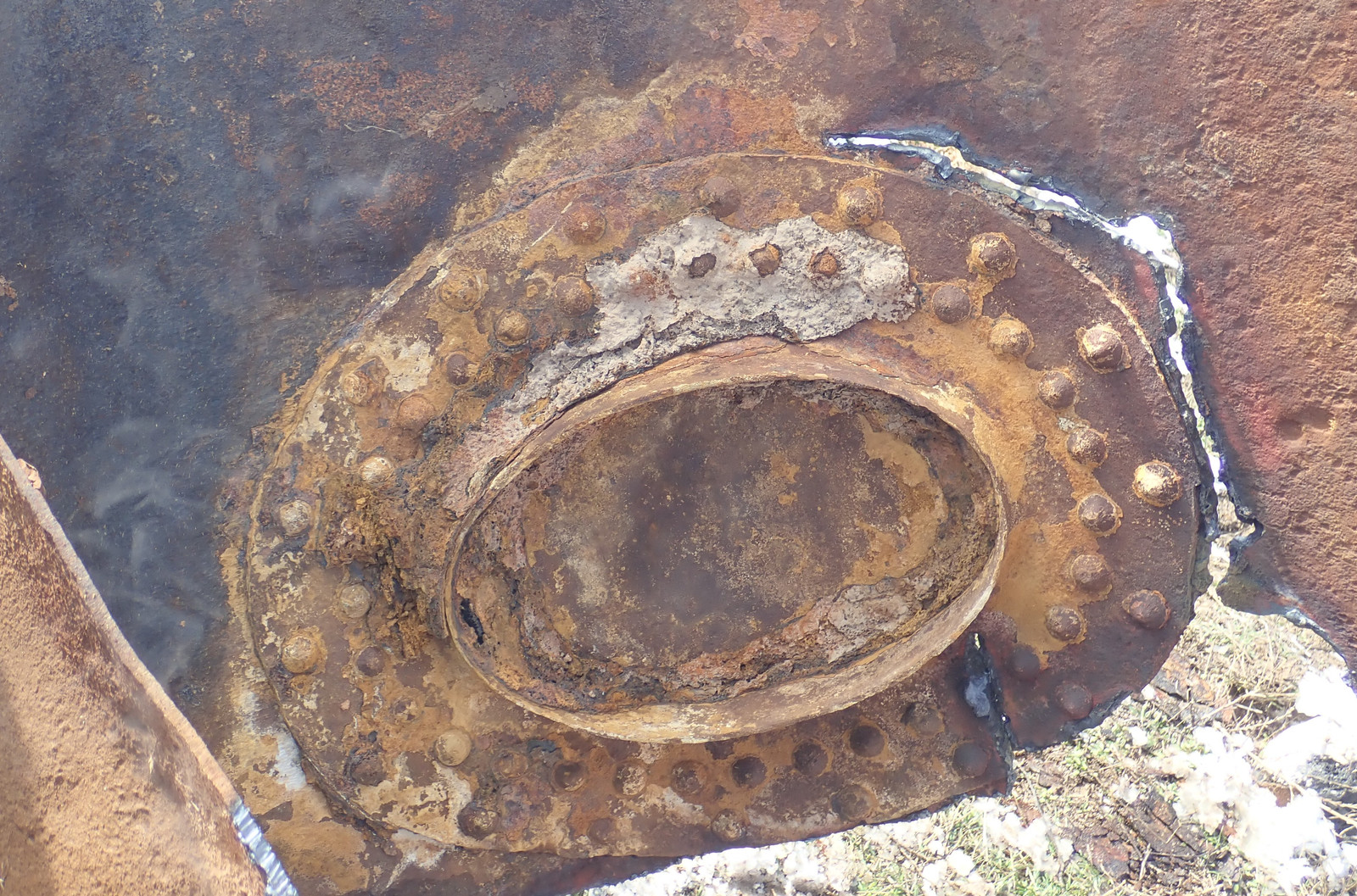
The next panel was somewhat faster, because there was interior access to scrape the back of the cut surface - so the torch was able to make far more steady progress. Once that panel was removed, we had access to shovel out the inside and prepare for the rest of the pieces to come apart.
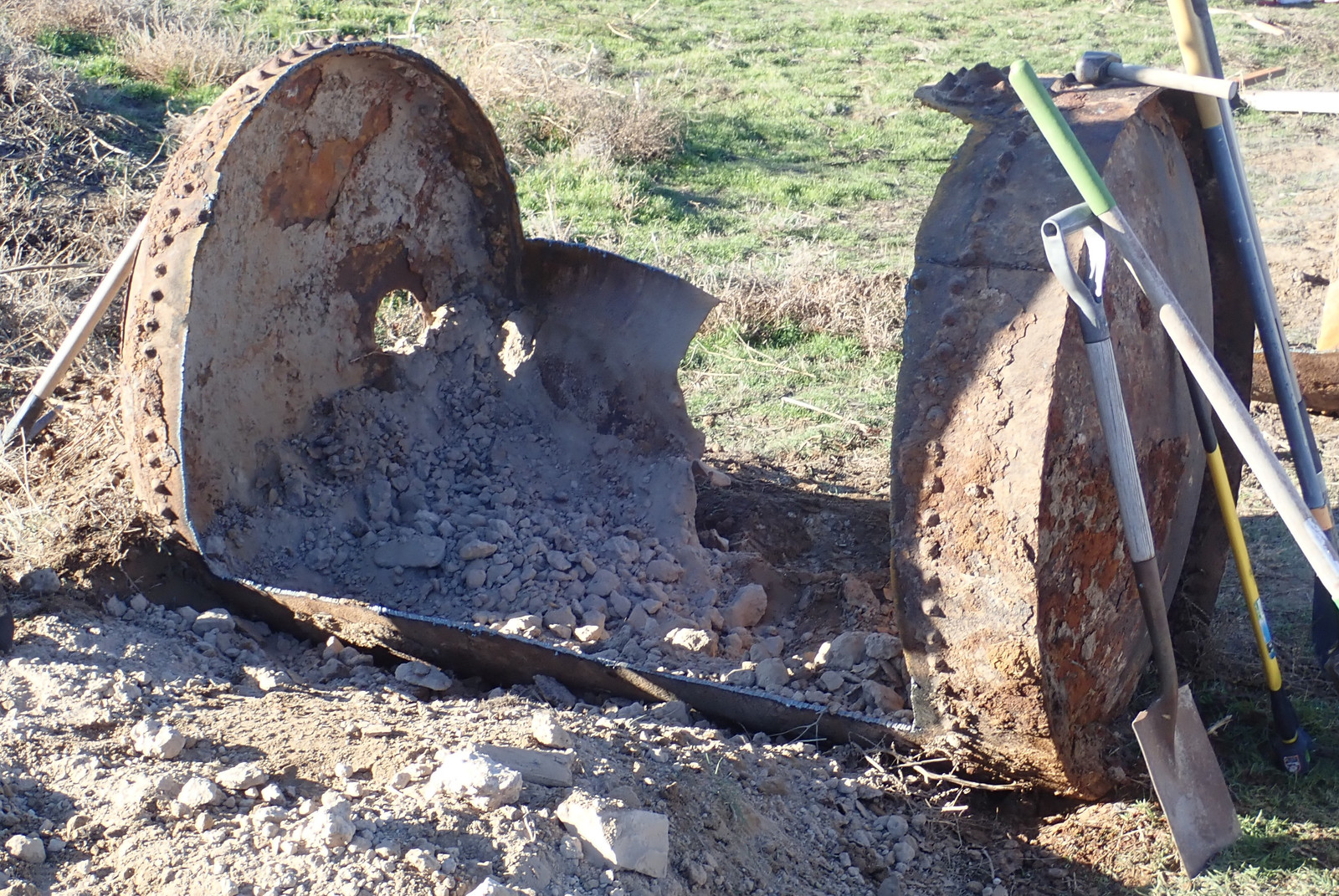
I’d assumed the contents would be rich soil. It wasn’t. It was mostly just dirt and rock that had fallen in through the open hatch over a period of many years. They were a compacted mess, which took some time to break up and get out - pickaxes remain handy things to have around.
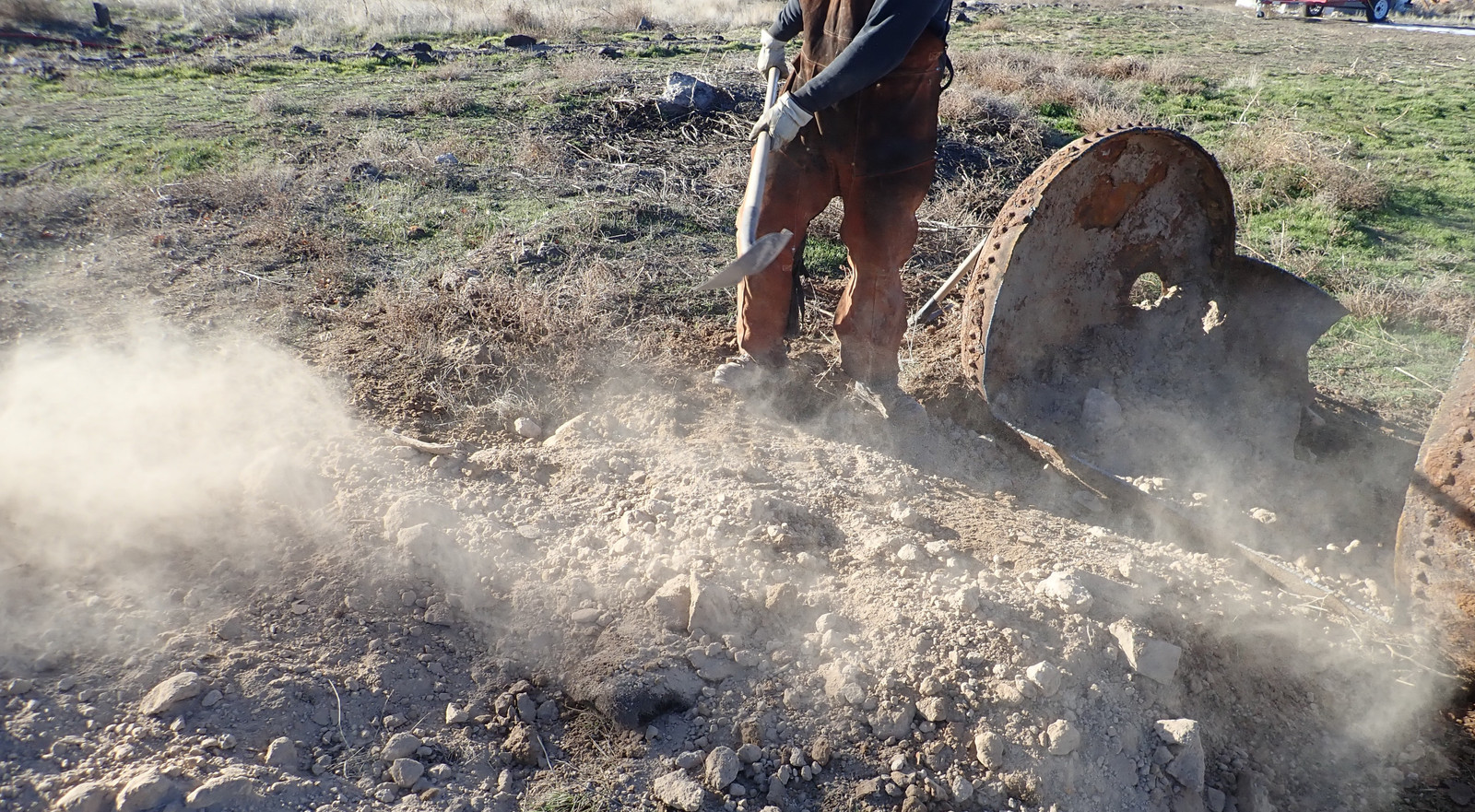
Another perk of the wintertime is that being dressed in welding gear isn’t as bad! I wasn’t nearly so protected, I just stayed out of the path of the sparks. Mostly.
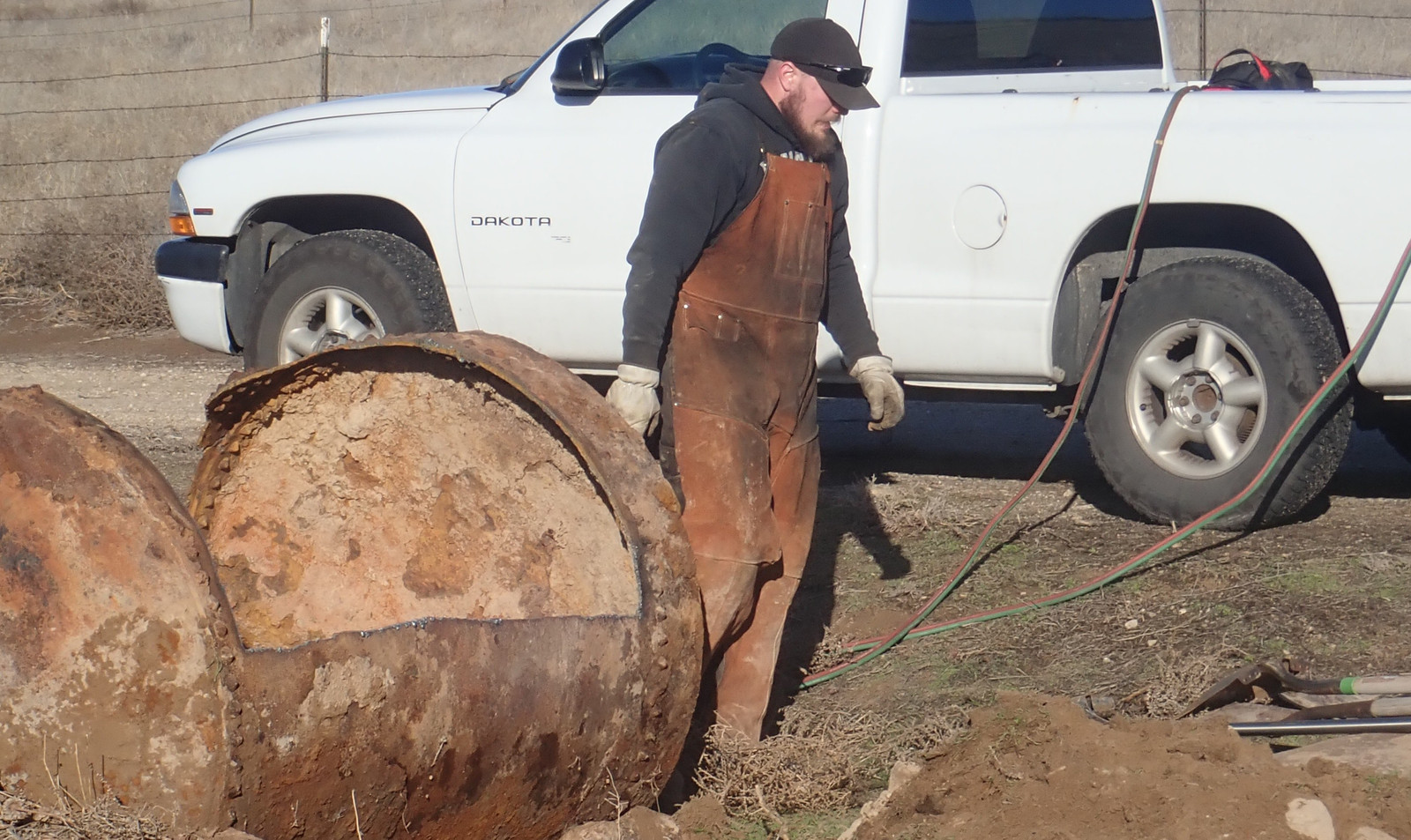
That “dent along the top” and slightly ripped metal is all that excavator was able to do to the tank. It took a decent bit of digging, rocking, and prying to convince the tank that it wanted to move from where it was.
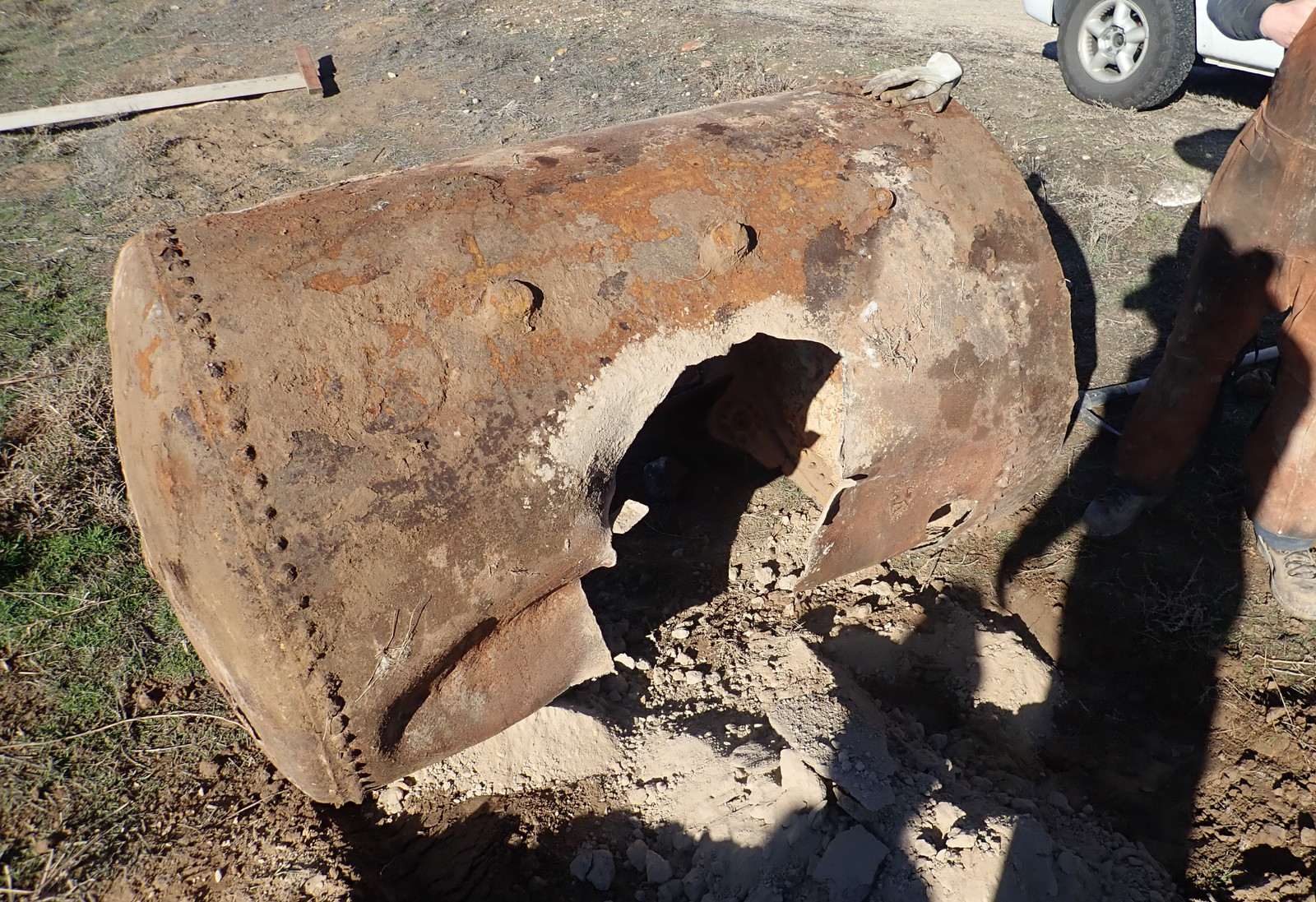
However, once upside down, a couple good blows with a sledgehammer freed up a lot of the remaining rock and dirt in it!
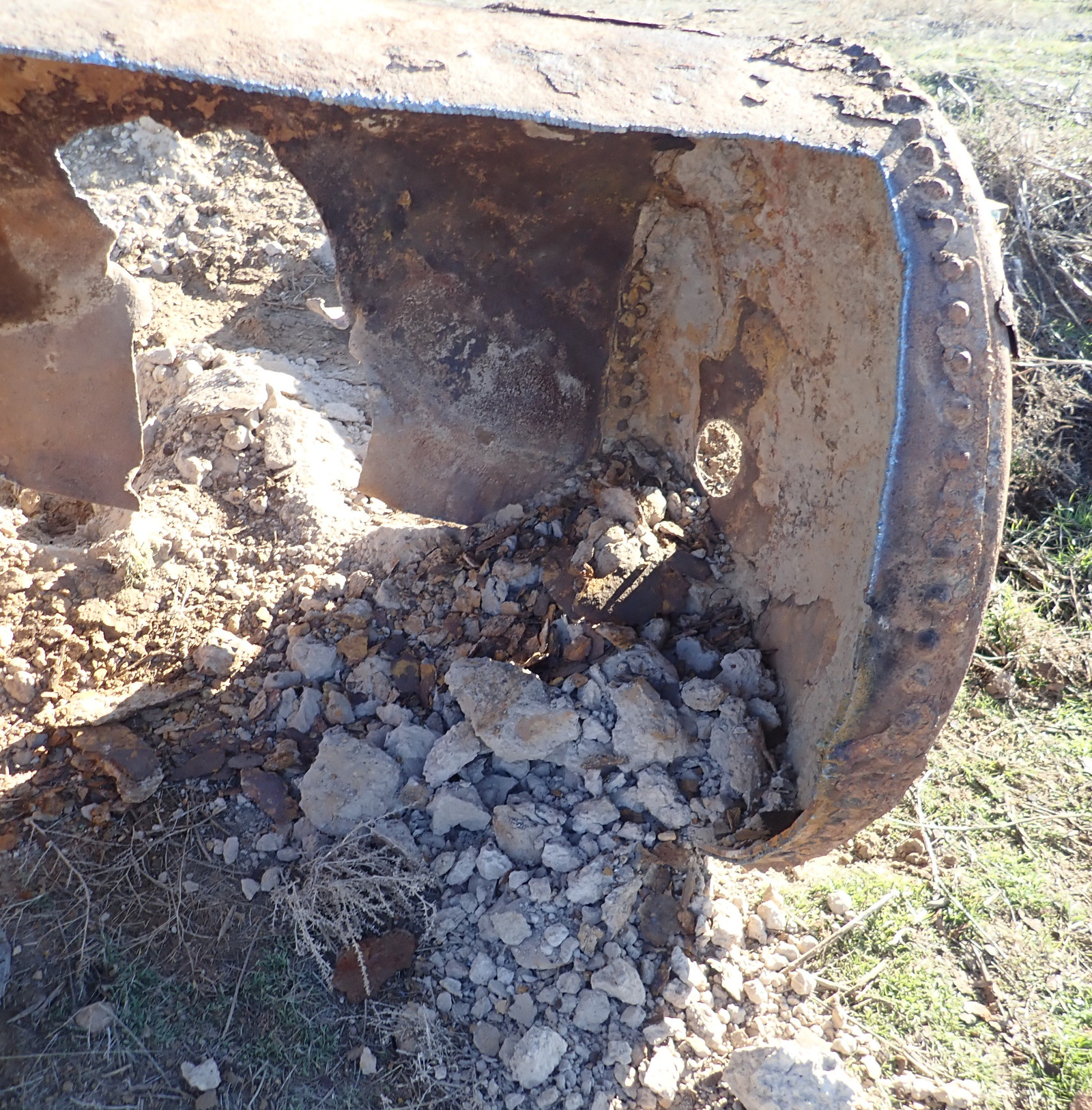
Cutting torches and grinders: Two good ways to light hills on fire. This sort of thing is why I waited until the hill was very wet to have someone come torch the tank apart. A cutting torch (at least this style) uses an oxy-acetylene flame to heat the metal up, and then a blast of oxygen to actually do the cutting - it burns the metal and clears the molten bits, and I understand that if you’re good and the metal is agreeable (this metal was assuredly not), you can turn off the acetylene after the cut is started and just run pure oxygen for the duration.
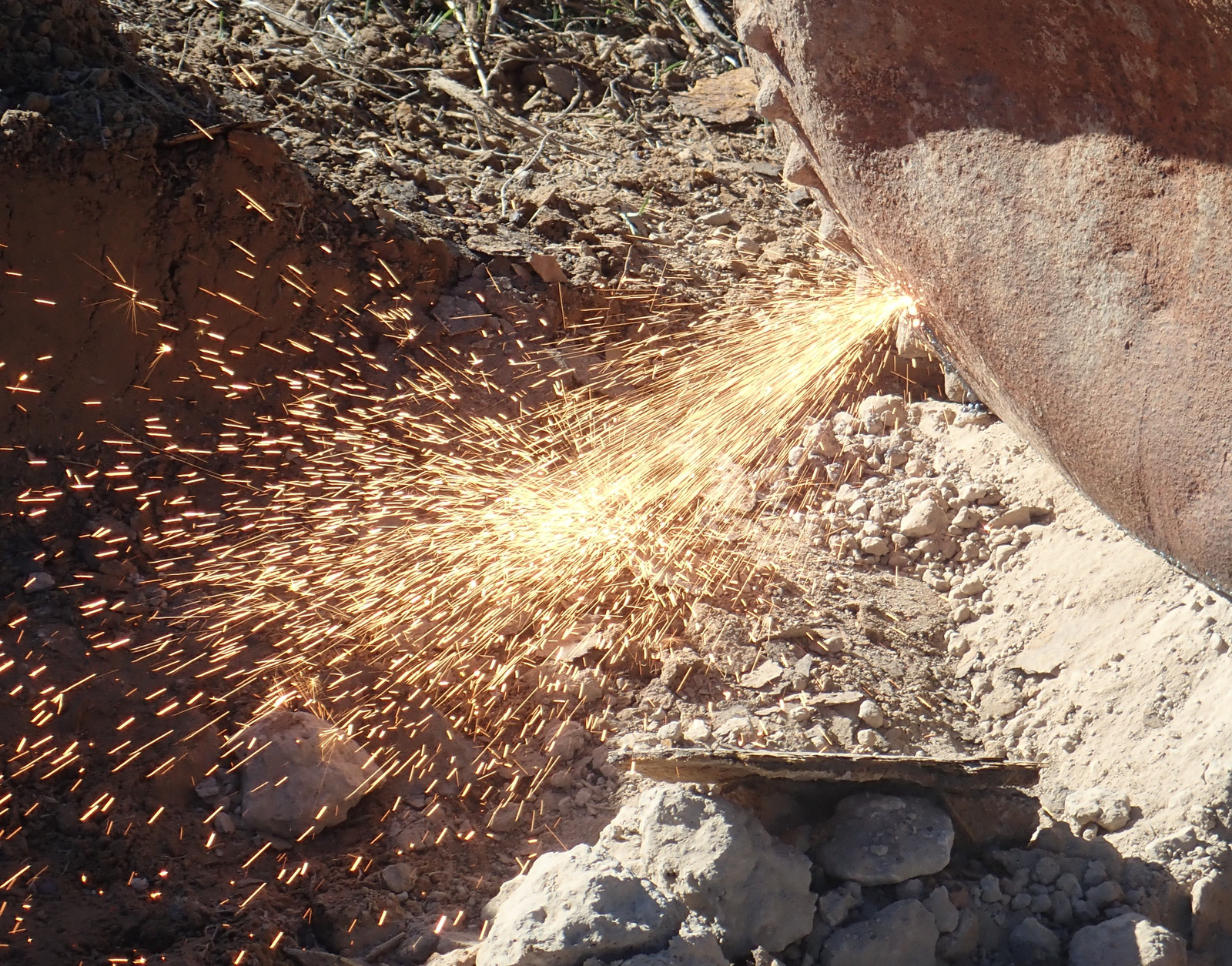
More than enough energy here to light off a dry hill. So I used a wet hill instead!
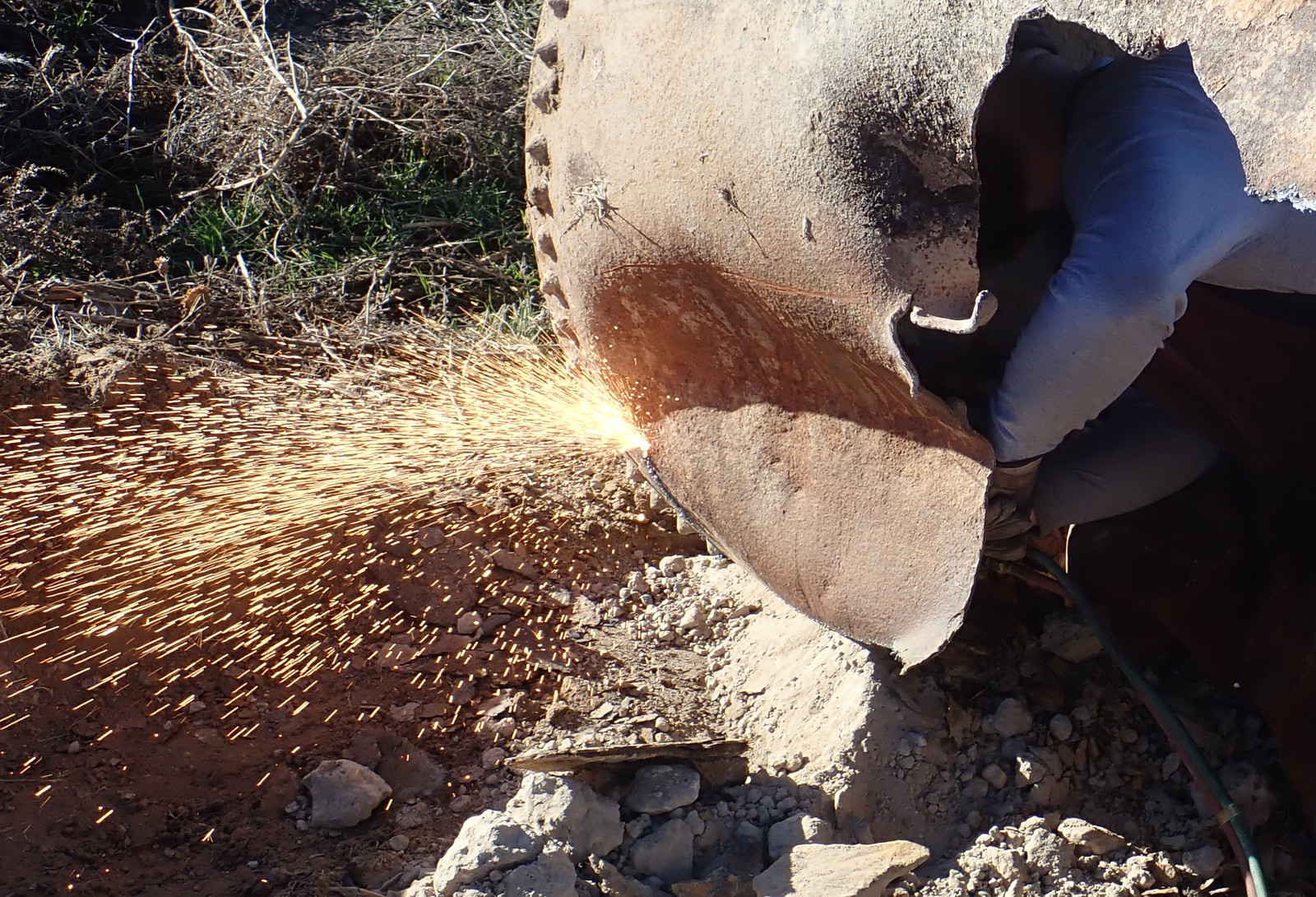
With another few panels cut out, there wasn’t that much remaining - just a fairly thin segment holding the two ends together.
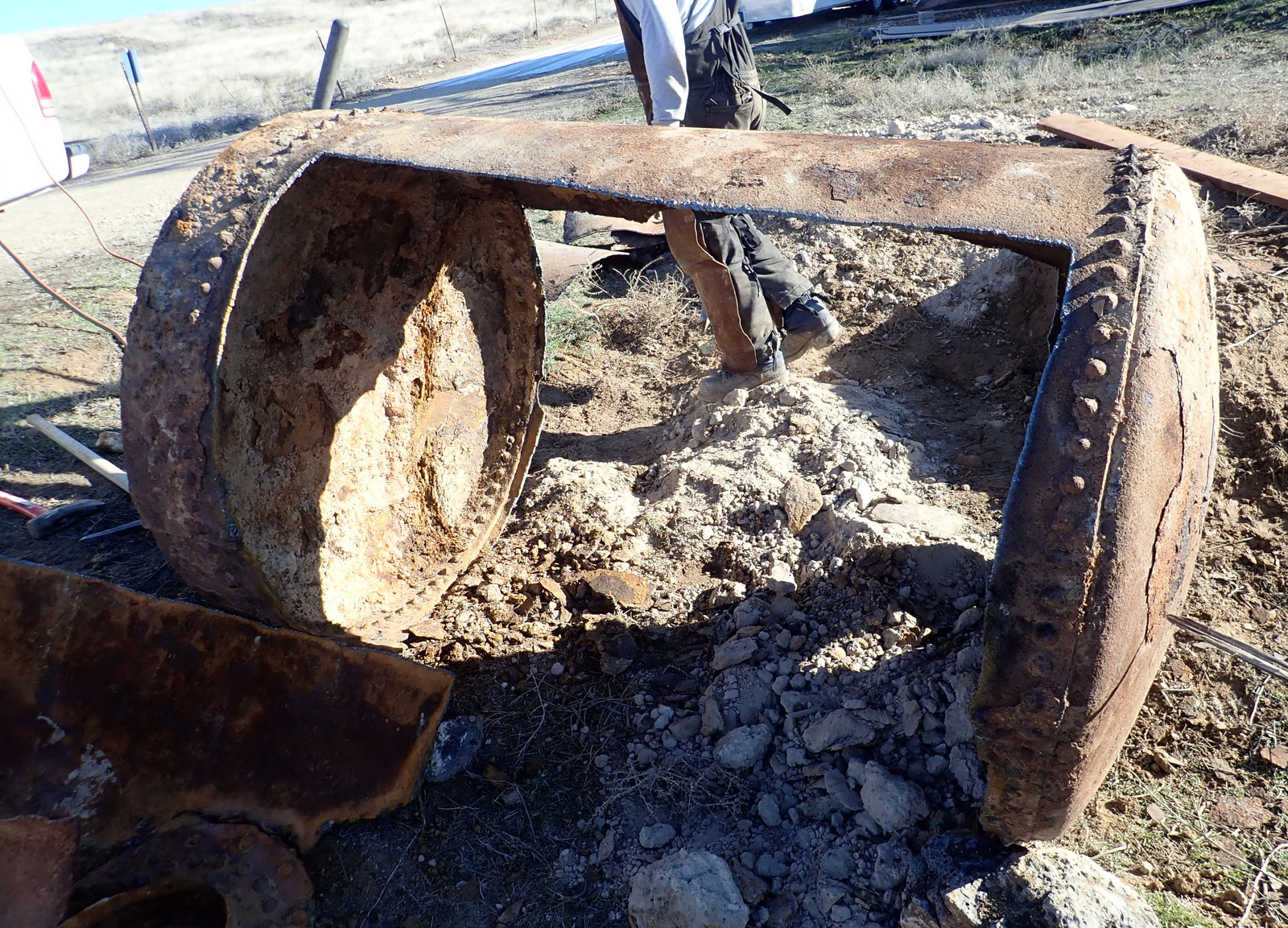
My son was out and about with us, and thought the whole process was fascinating. Hammers, torches, metal… this is his idea of a good time!
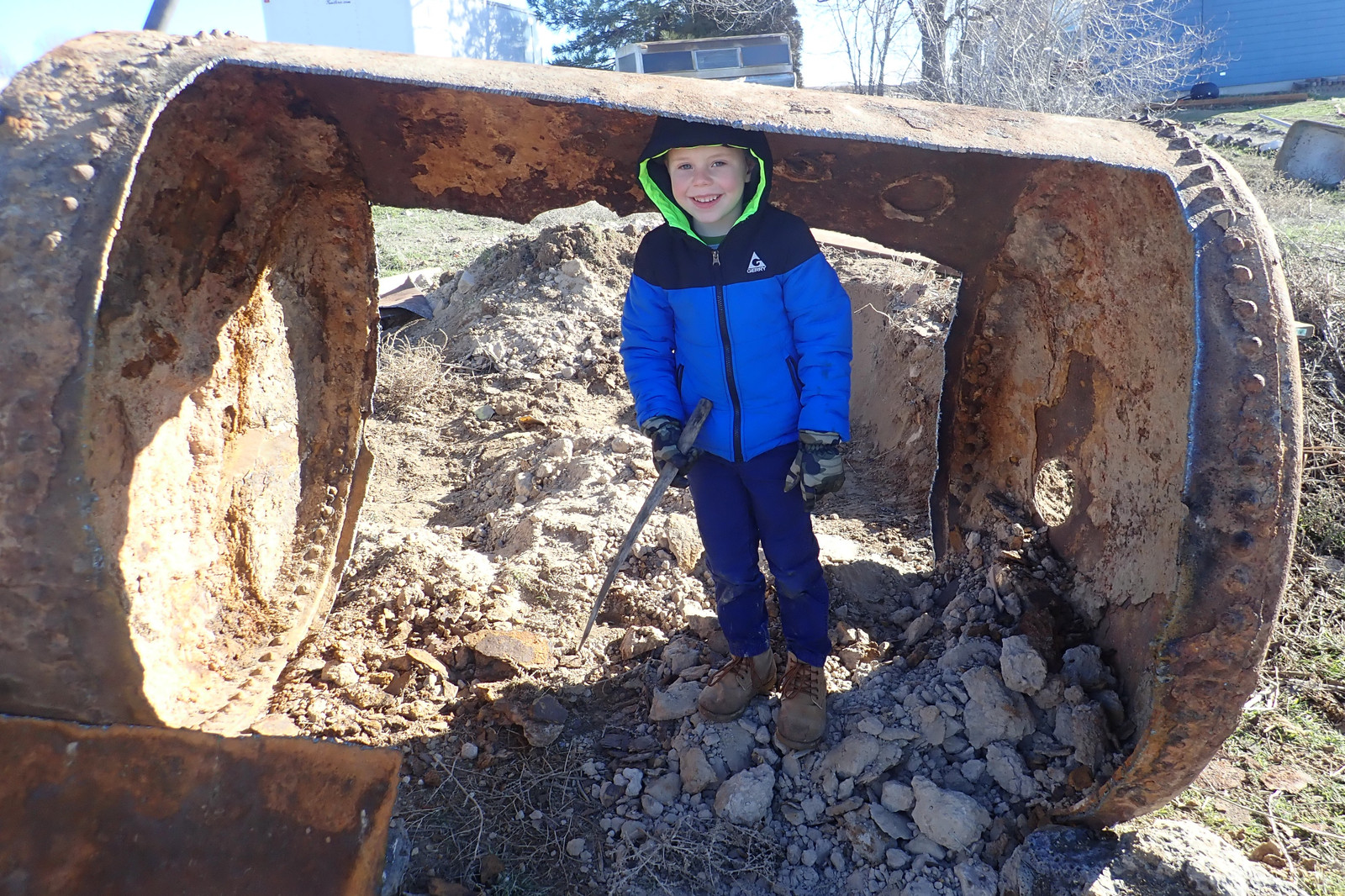
With the first cut nearly done, the metal was ready to drop, and everyone was out of the way. Going…
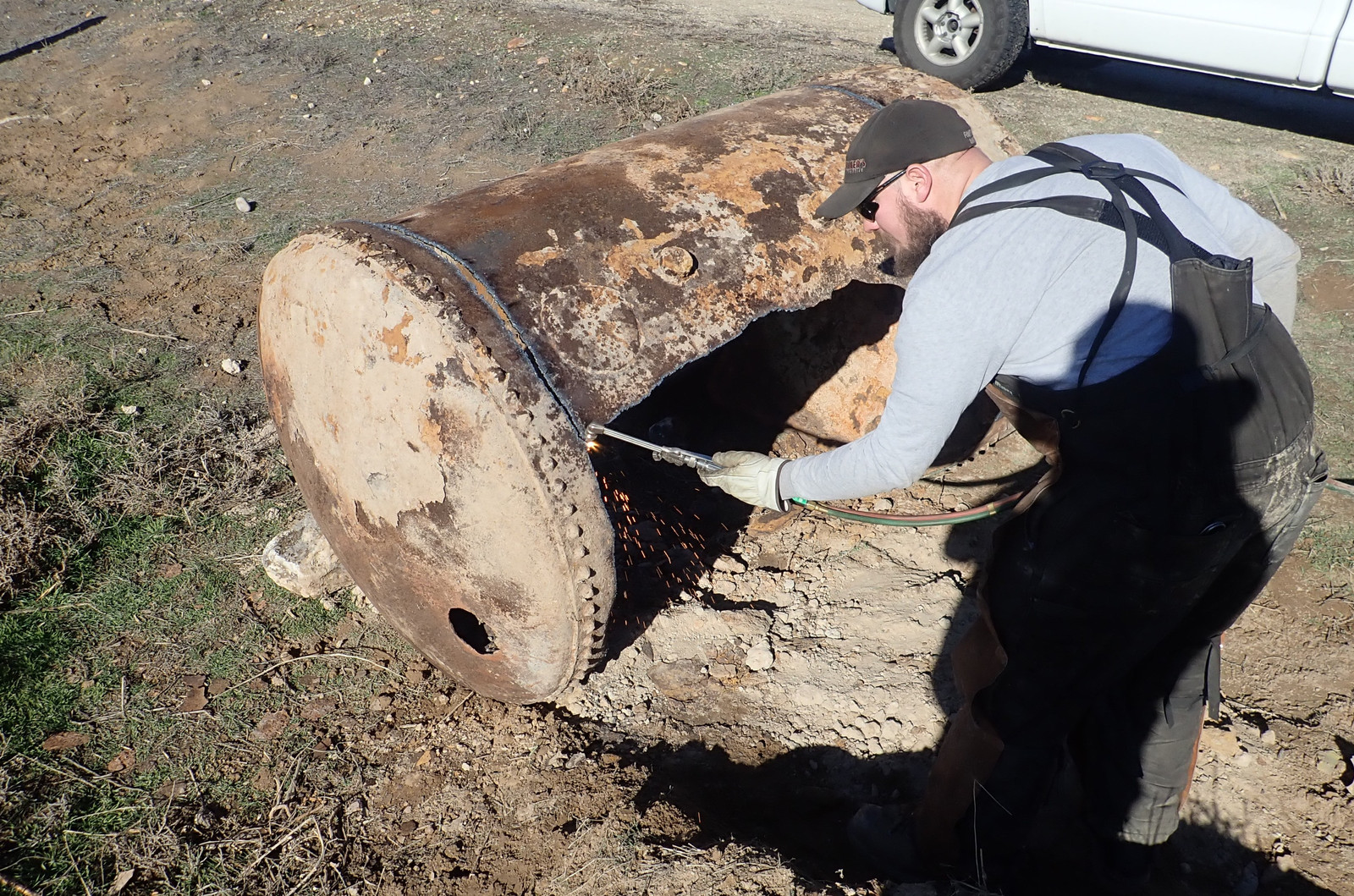
Going…
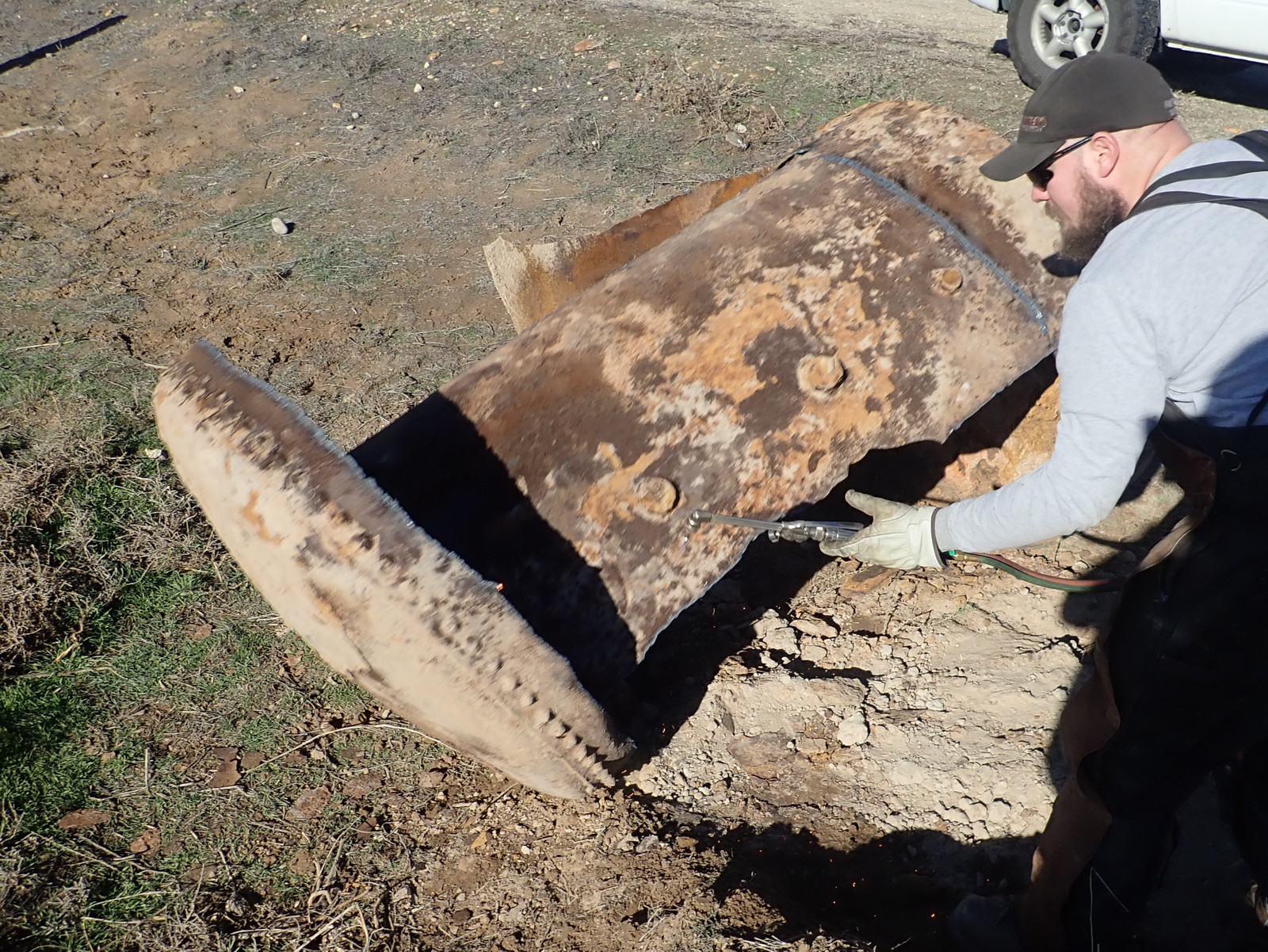
Gone!
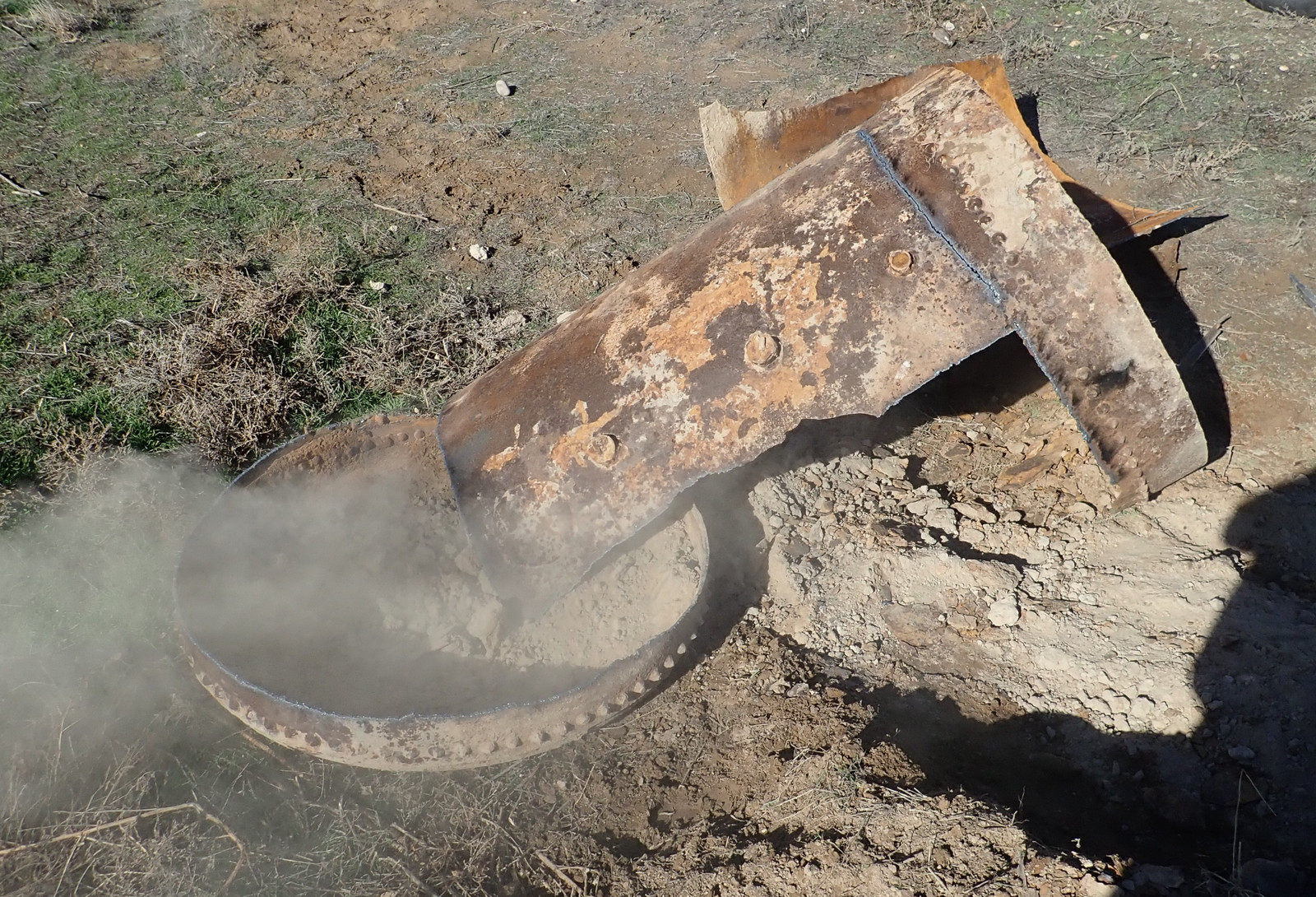
You can see the riveted construction of the end caps too - a massive overlap between the tank body and the end caps, with a ton of rivets pounded in place. Those rivets would have been red hot as they were installed, with a bucking bar on the inside as someone pounded them into shape.
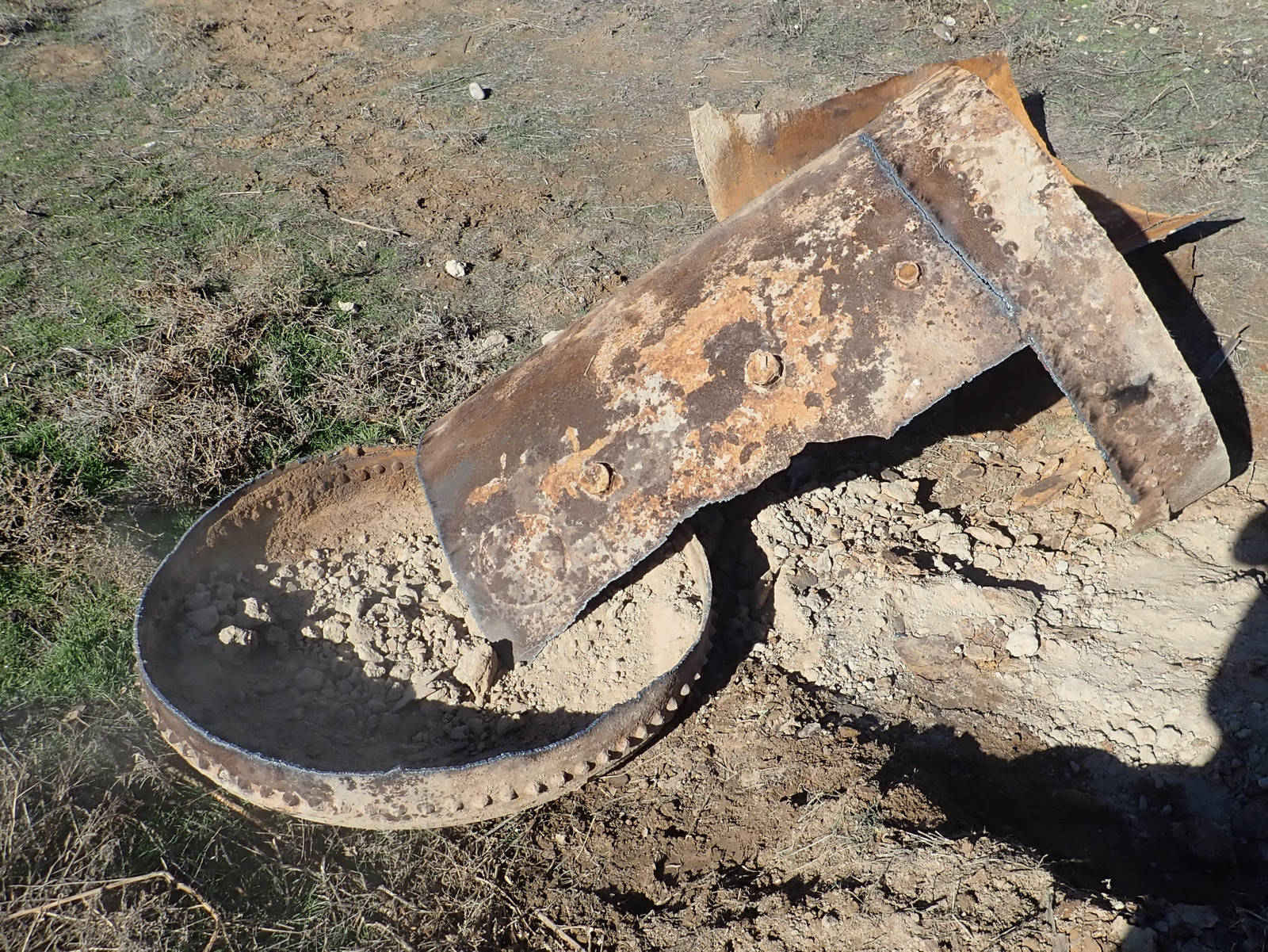
Finally, we stood the tank up and dropped the last piece.
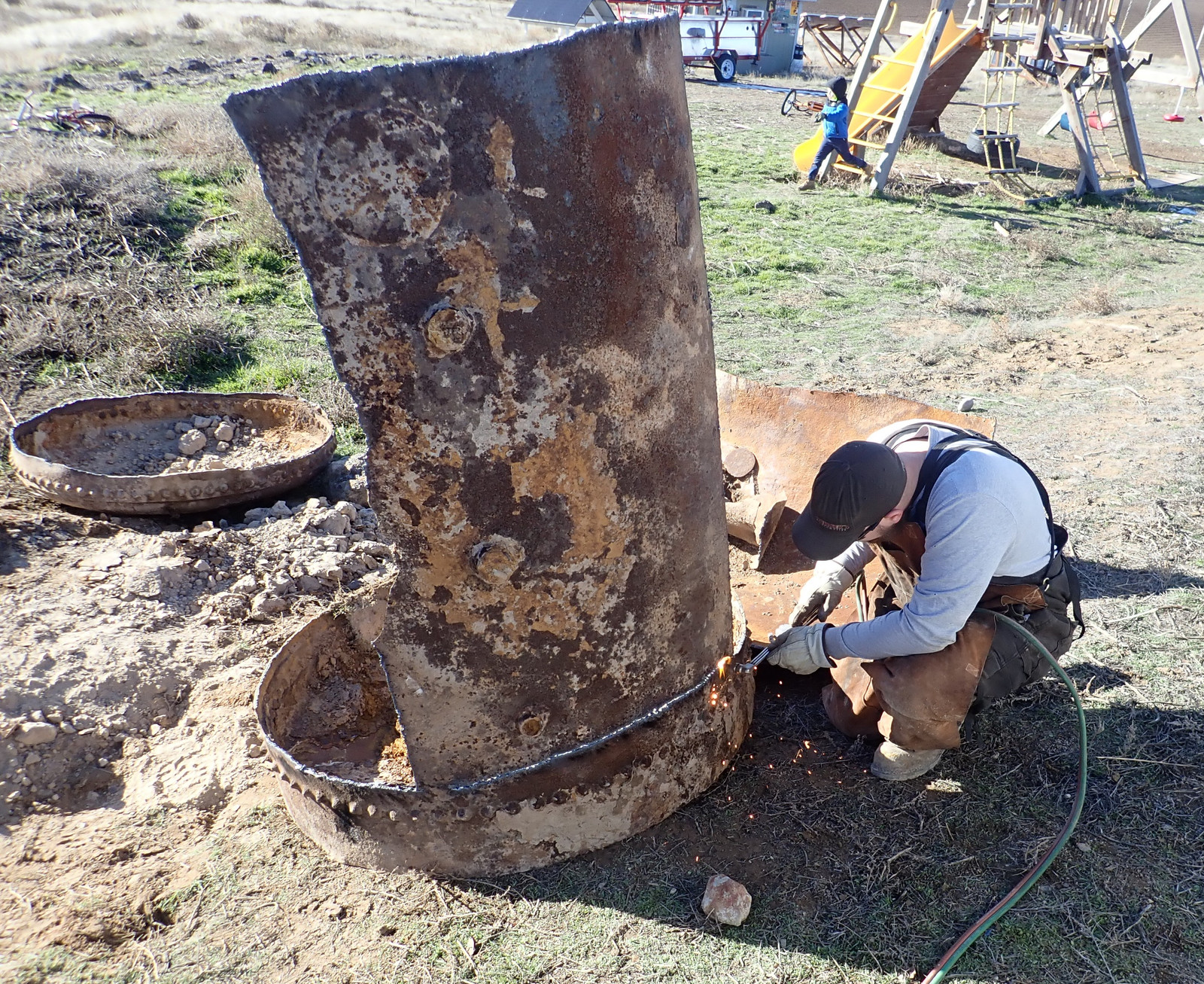
Josh earned this one. It was a crappy cutting tank, it kept clogging the tip with back splatter, and he went through about a full tank of oxygen getting this apart - but, importantly, it’s apart now!

Loading and Hauling
Unfortunately, instead of being “one tank laying around,” it’s now “a lot of pieces of tank laying around.” And that is best solved by a run to the scrap yard. As much as “random ancient plate iron” might be useful to some people, it’s not useful to me, the iron is not in good shape, and I just want it gone. Pieces were sized to be loadable by “a few guys lifting” - so, one particular Monday evening lifegroup after things had dried up, I brought the trailer up, handed out work gloves, and a few people got to work.
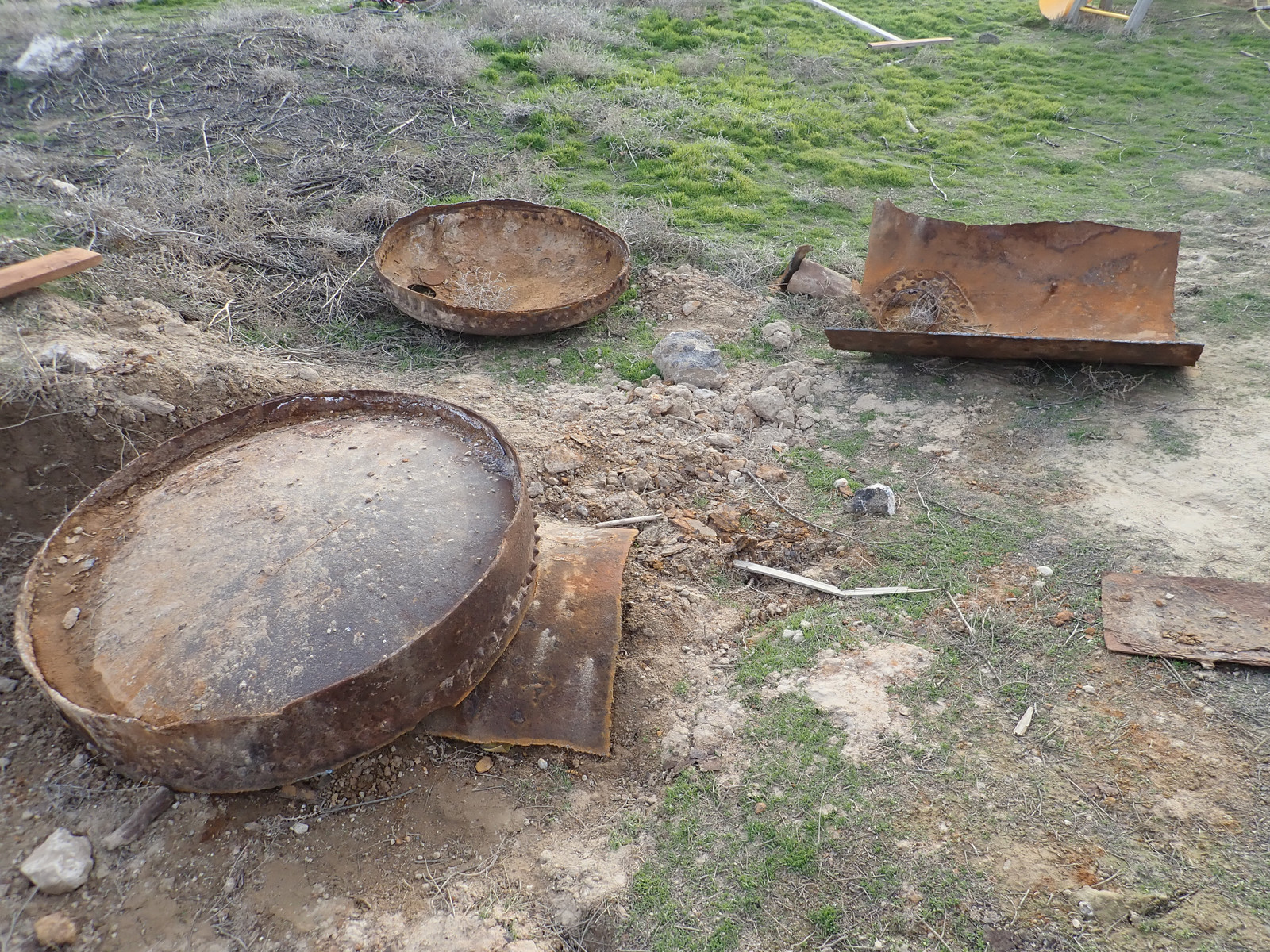
I was more than happy to help out, but like many other things in life, sometimes all you need is the right person. In this case, his name is Bill, and he spends a lot of his free time at the gym lifting and moving heavy things. These pieces qualify.

When someone with several hundred pounds of scrap iron suggests everyone else get out of the way, the right answer is to get out of the way and let them do their thing!
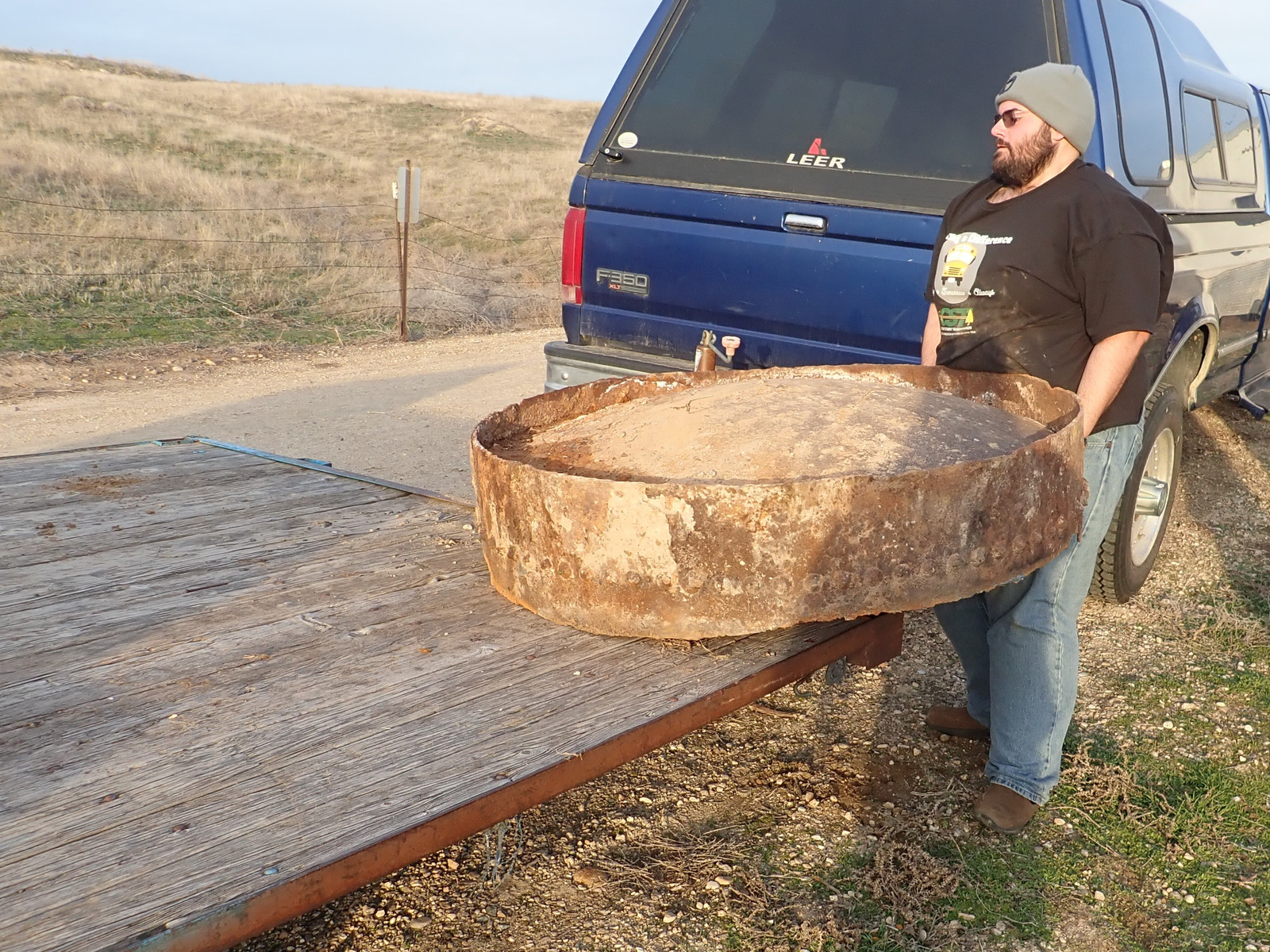
This trailer likes to be loaded “heavy in the front,” so the big pieces just stacked up there. The deck on this trailer is on my list of things to redo at some point - I have plans to go through the trailer and fully restore it back to fully operational. Some of the stuff like the tilting feature have been disabled over the years, and it would be nice to have effective trailer brakes with how much weight is on this trailer at some points.
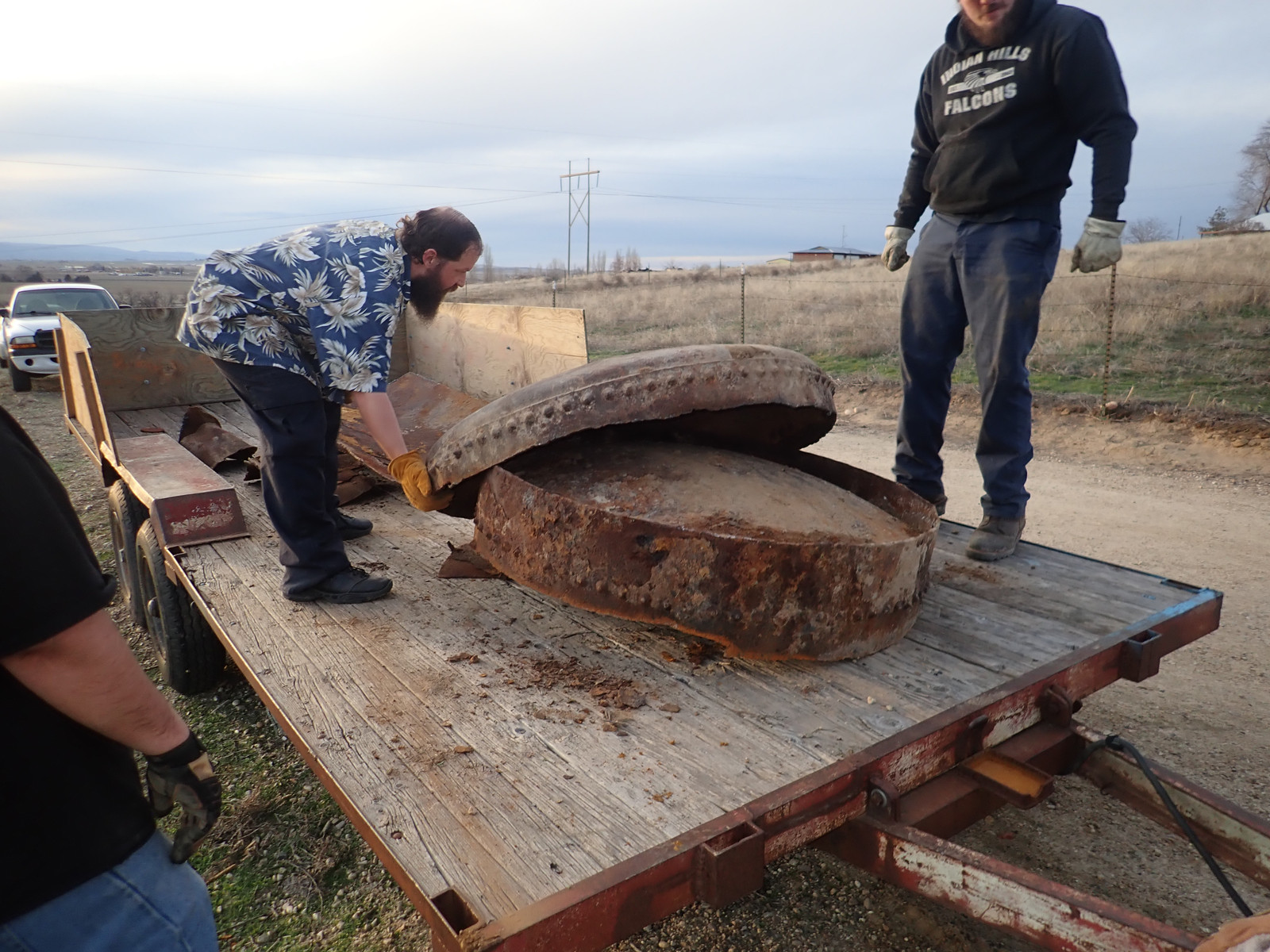
Collaborative “walking” of the remaining piece solved quite a bit as well.
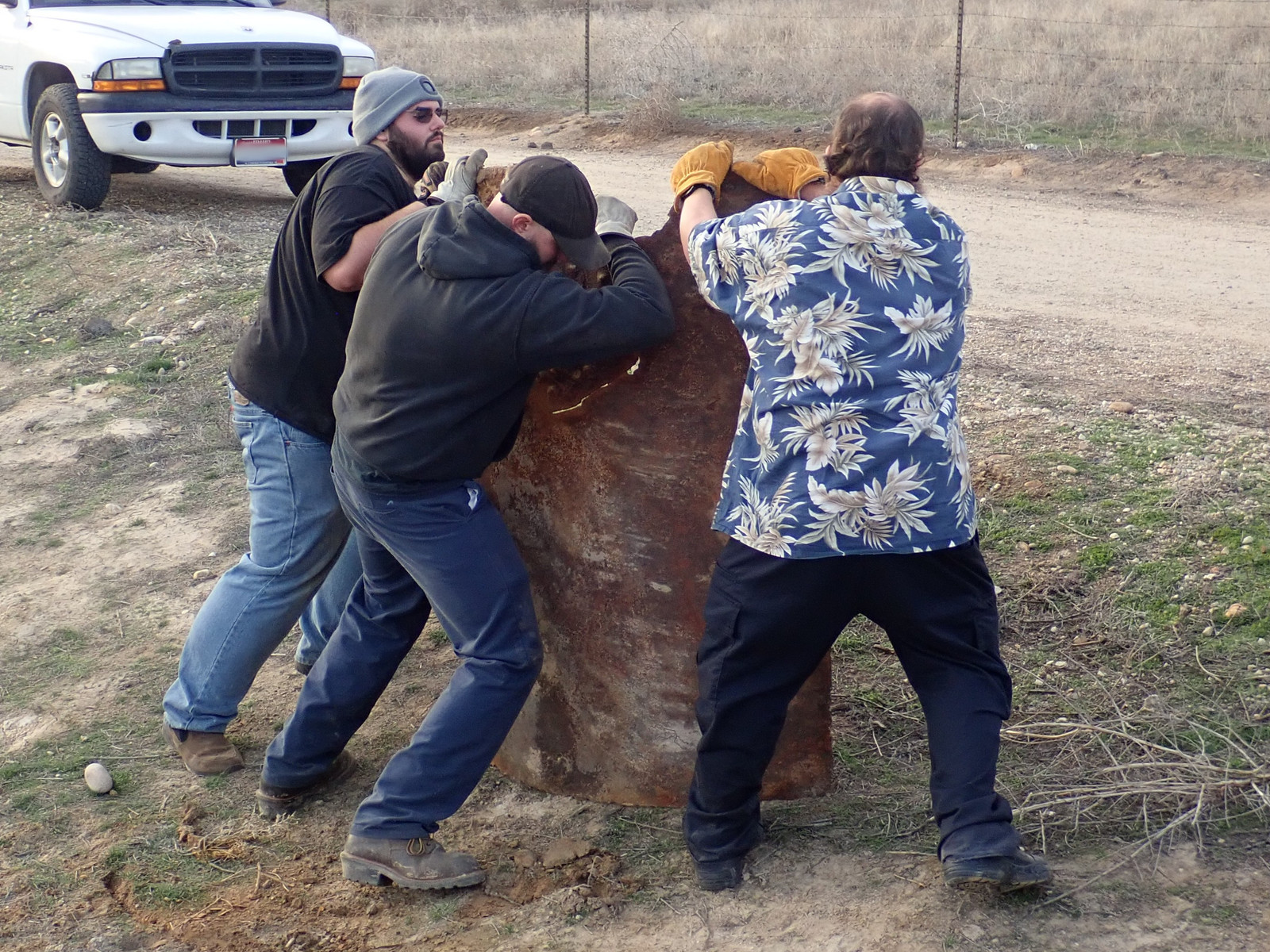
Project Completed!
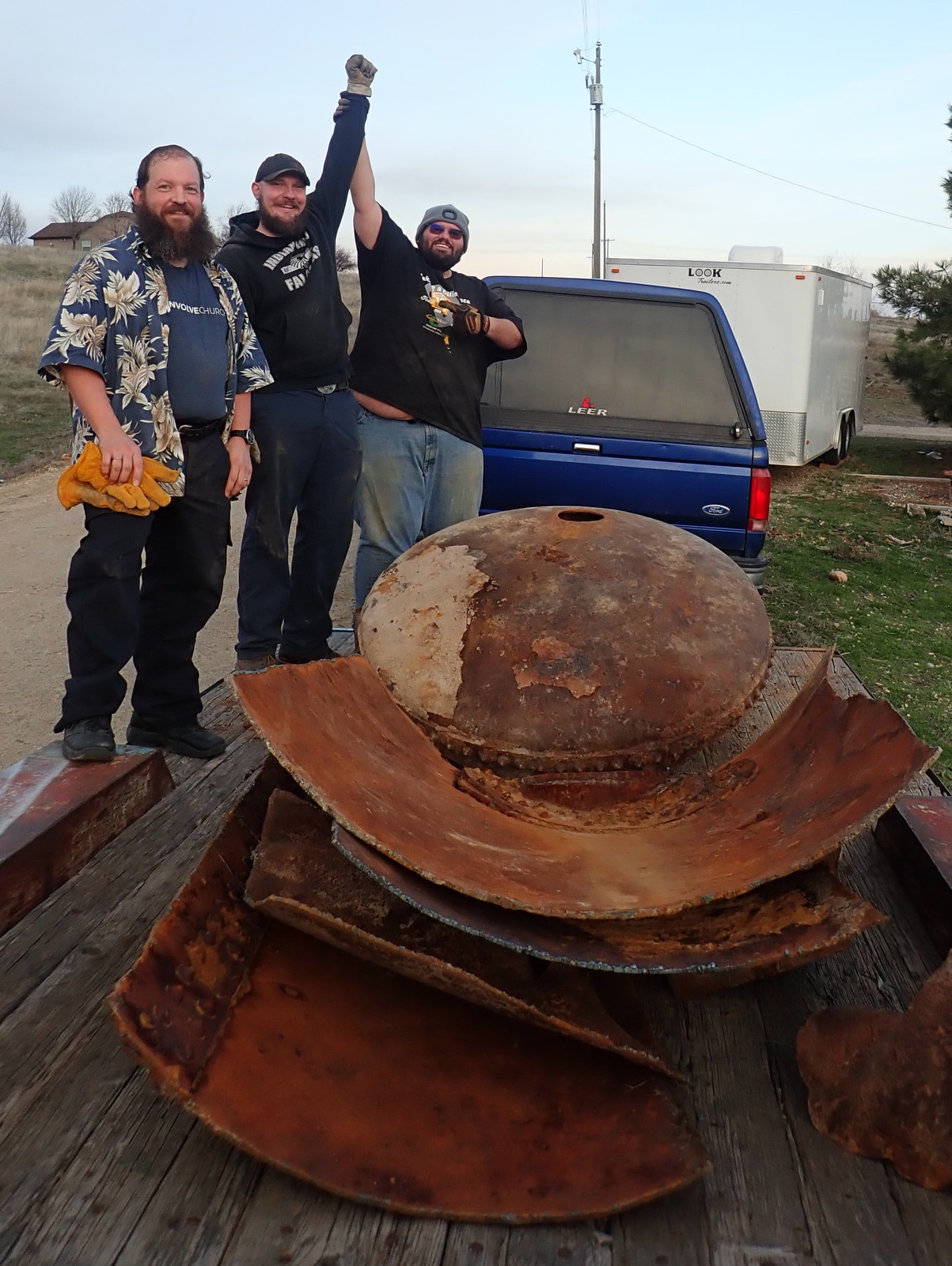
Unloading at the Scrapyard
I strapped the pieces down well enough to transport, and hauled them into the local scrapyard - which was an absolute mudpit, after the rain we’ve had lately. Oh well. If you’ve never hauled scrap before, you might wonder how it’s unloaded - the pieces obviously take several people to move easily. Fortunately, this is a very well solved problem, and if you’ve ever seen movies with junk yards, you’ve probably got a good idea as to how this all works out. My son came with me, and instead of letting him be covered in mud (which he would love and I would have to clean out of my truck), I set him in the pickup bed to watch the process.
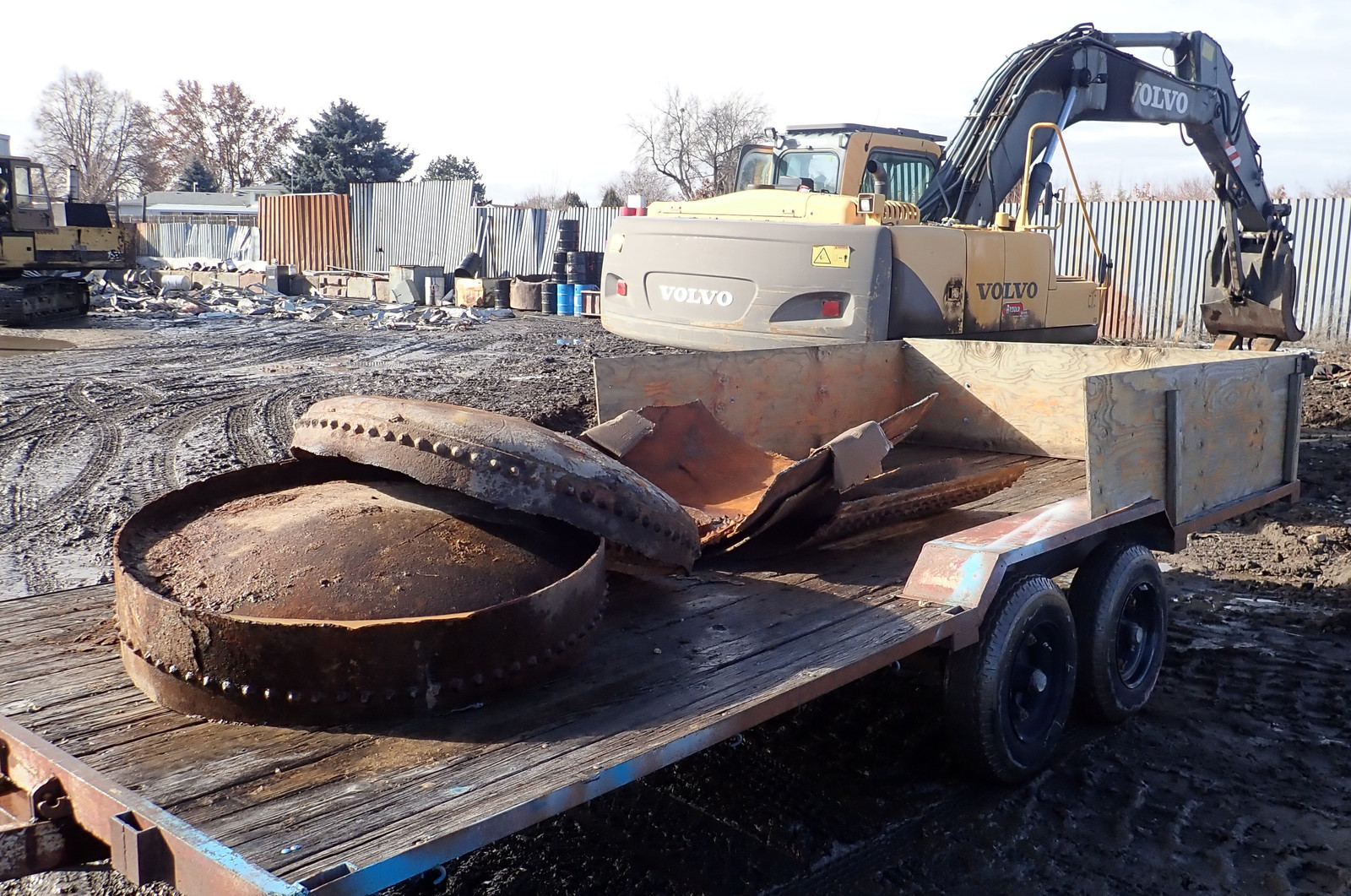
A big electromagnet on big machinery! They’ve got a magnet chained up to an excavator, and it sucks the metal up. I’m amazed at just how strong it is - it grabs stuff by the edge without any trouble.
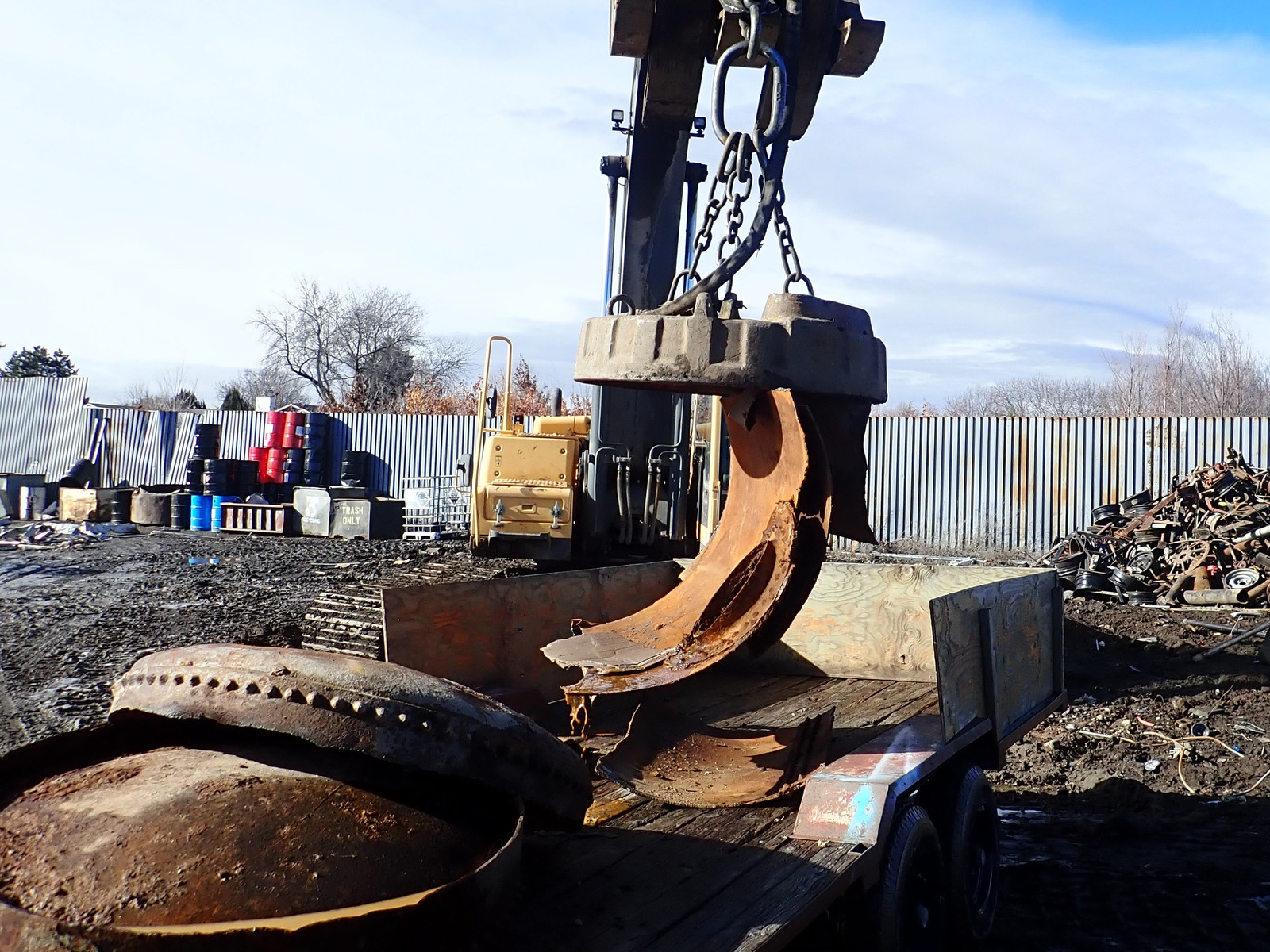
What’s nearly half a ton of endplates to an excavator? It just solved the problem perfectly.
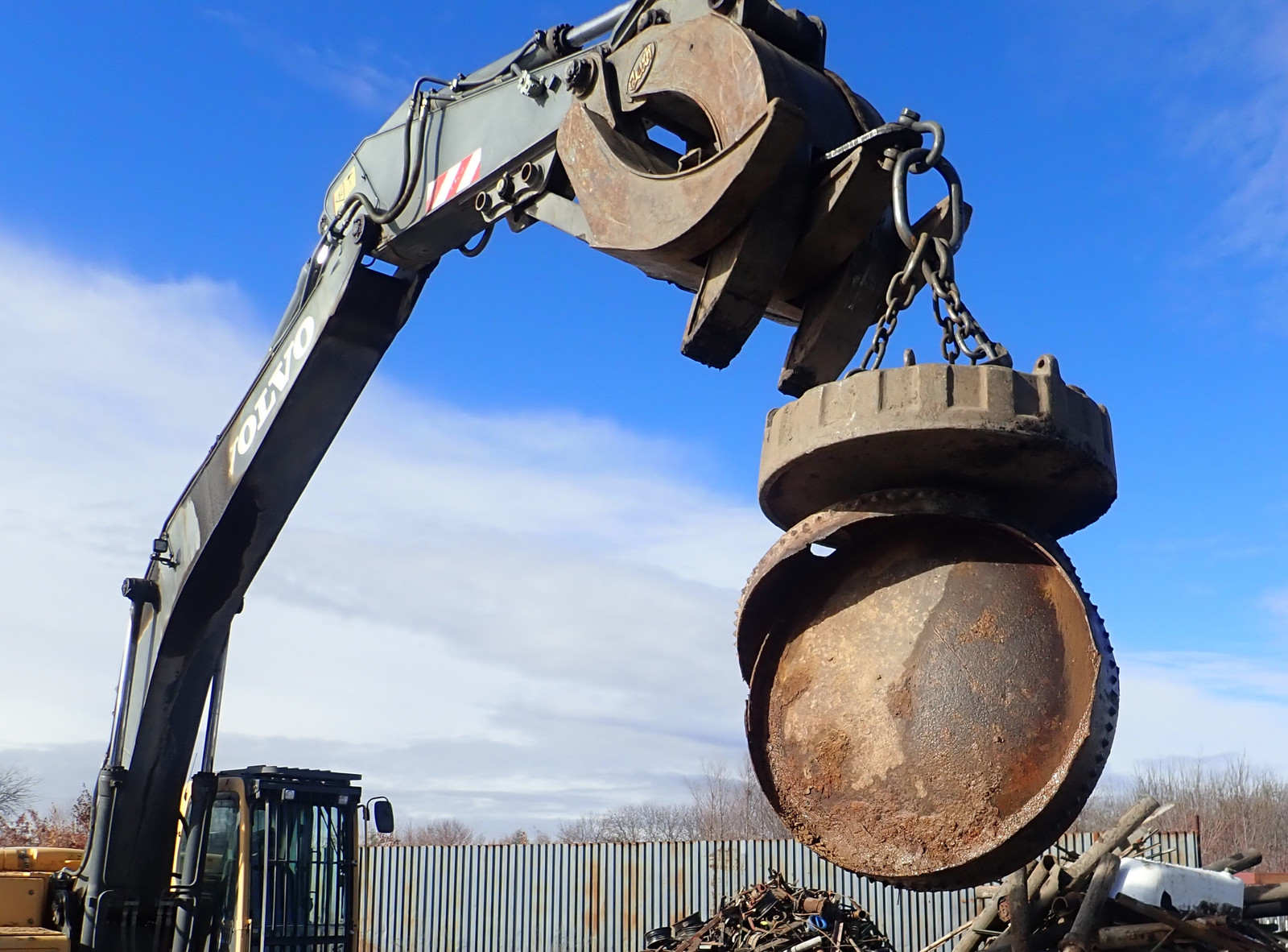
And afterwards, they even sweep the trailer for loose magnetic debris! Dragging the magnet across the bed gets quite a bit of loose scrap too.
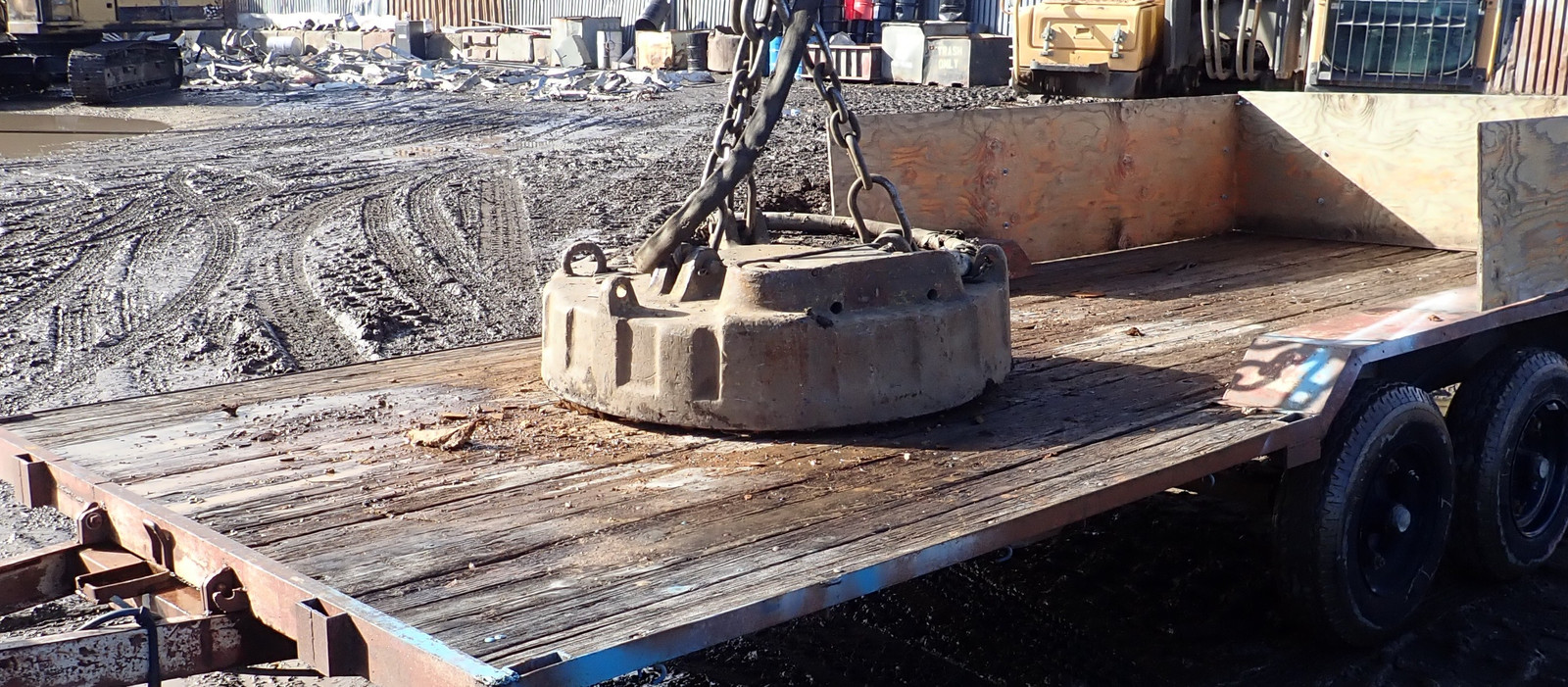
Anyway, that’s 1400 pounds of scrap iron cut up and off the hill!
And if you’re in the Treasure Valley and need random work done, call Josh!
Comments
Comments are handled on my Discourse forum - you'll need to create an account there to post comments.If you've found this post useful, insightful, or informative, why not support me on Ko-fi? And if you'd like to be notified of new posts (I post every two weeks), you can follow my blog via email! Of course, if you like RSS, I support that too.